The U.S. Environmental Protection Agency’s (EPA) energy guide, Energy Efficiency Improvement and Cost Saving Opportunities for Cement Making, discusses energy efficiency practices and technologies that can be implemented in cement manufacturing plants. This ENERGY STAR guide provides current real world examples of cement plants saving energy and reducing cost and carbon dioxide emissions.
Cement
Cement is a binding agent and is a key ingredient of the most used man-made material: concrete. The demand for cement is strongly correlated to the rate of economic development. Cement manufacturing is the third largest energy consuming and CO2 emitting sector, with an estimated 1.9 Gt of CO2 emissions from thermal energy consumption and production processes in 2006.1 If Best Available Technologies can be adopted in all cement plants, global energy intensity can be reduced by 1.1 GJ/t-cement, from its current average value of 3.5 GJ/t-cement. This would result in CO2 savings of around 119 Mt.2
Dry, semi-dry, semi-wet and wet processes are the four main process routes that are used for the production of cement. Dry processes are considerably more energy efficient but the choice of technology mainly depends on the state of raw materials. Thanks to the availability of dry materials a great share of production in the developed world is today converted to dry processes. Dry processes are also the choice for new plants or for those looking for expansions or upgrades. The energy-intensive wet process is still used in some countries (and is a considerable share of production in the Former Soviet Union, Australia, and New Zealand), but is being phased out in many countries.
Most of the energy use and CO2 emissions of the cement industry is linked to the production of clinker, which is the main component of cement and produced by sintering limestone and clay. Electricity needed for crushing and grinding raw materials, fuel, and the finished products represents another important energy demand. Proven technical options with potential to enable considerable reductions in energy use and CO2 emissions can be categorized into: use of energy efficient technologies; use of alternative raw materials and fuels, and reducing the clinker content of cement via increased use of other blends. There are also emerging options in the form of alternative cementitious materials and carbon capture and storage.
CementSchematic
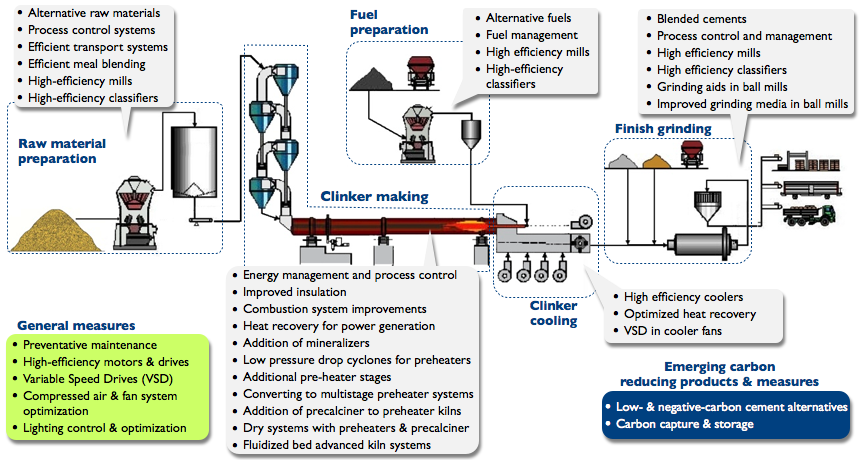
CementProcesses
Cross-Sectoral Systems
Selected Cement Technologies & Measures
For a wider list of technologies & measures, please follow the links under processes above.
Products
- Clinker
- Cement
Cement Publications
Energy Efficiency Improvement Opportunities for the Cement Industry
Development of State of the Art Techniques in Cement Manufacturing: Trying to Look Ahead
The report represents the independent research efforts of the European Cement Research Academy (ECRA) to identify, describe and evaluate technologies which may contribute to increase energy efficiency and to reduce greenhouse gas emissions from global cement production today as well as in the medium and long-term future.
Energy Efficiency and Resource Saving Technologies in Cement Industry
This Cement technologies booklet was compiled by the APP Cement Task Force (CTF) through one of its activities to help its member countries share information on all available energy efficient technologies generally used in the world’s cement industry. The document offers a comprehensive compilation of commercially-available energy efficient technologies used in the cement industry.
International Best Practices for Pre- Processing and Co-Processing Municipal Solid Waste and Sewage Sludge in the Cement Industry
Date:
Format:
Type:
This report describes international best practices for pre-processing and co-processing of municipal solid waste and sewage sludge in cement plants, for the benefit of countries that wish to develop co-processing capacity. The report is divided into three main sections, concentrating on: a) fundamentals of co-processing; b) examples of international regulatory and institutional frameworks for co-processing, and; c) international best practices related to the technological aspects of co-processing.
Cement Tools
Cement Manufacturing Energy Performance Indicator Tool
Date:
Source:
Format:
Type:
Developed by the United States Environmental Protection Agency, the ENERGY STAR Cement Plant Energy Performance Indicator (EPI) is a statistical model that allows cement manufacturing plants located in the US to benchmark their energy performance against the industry. Annual plant energy and operating data is entered into the model to receive an energy efficiency score on a scale of 1 to 100.
Benchmarking and Energy Saving Tool (BEST) for Cement
Benchmarking and Energy Saving Tool (BEST) for Cement is a process-level benchmarking tool developed by Lawrence Berkeley National Laboratory and Energy Research Institute in China.
Sewage Sludge Use in Cement Companies as an Energy Source (SUCCESS) Tool
This Excel-based tool serves to assist decision makers in implementing sludge-end-use-in-cement schemes with optimal economic and environmental outcomes. The environmental and economic costs and benefits associated with burning sewage sludge in cement kilns will vary based on the energy content of the sludge (lower heating value) and the transportation distance between the wastewater treatment plant and proposed cement plant.
Depending on the employed production technology, characteristics of raw materials, and the composition of final products cement manufacturing can show significant variations in energy consumption and CO2 emissions. In the following, best attainable values for different production processes and for different cement products are presented.
CementBenchmarks
Production Process | Energy Consumption (GJ/t Clinker) | |
---|---|---|
Min | Max | |
Dry, multistage cyclone pre-heater and pre-calciner kilns | 2.85 | 3.0 |
Dry process rotary kilns with cyclone pre-heaters | 3.1 | 4.2 |
Semi-dry/semi-wet processes (Lepol kiln) | 3.3 | 4.5 |
Dry process long kilns | 5.0 | |
Wet process long kilns | 5.0 | 6.0 |
Shaft kilns (up to 100 t/d capacity) | 3.1 | 4.2 |
Process | Energy carrier | Product unit | kWh/t product | GJ/t prduct | kWh/t clinker | GJ/t clinker | kWh/t cement | GJ/t cement |
---|---|---|---|---|---|---|---|---|
Raw materials preparation | Electricity | t raw meal | 12.05 | 0.04 | 21.3 | 0.08 | 20.3 | 0.07 |
Solid fuels preparation | Electricity | t coal | 10 | 0.04 | 0.97 | 0.92 | ||
Clinker making | Fuel | t clinker | 2.85 | 2.71 | ||||
Electricity | t clinker | 22.5 | 0.08 | 21.4 | 0.08 | |||
Additives preparation | Fuel | t additive | ||||||
Electricity | t additive | |||||||
Finish grinding | ||||||||
325 cement | Electricity | t cement | 16 | 0.06 | ||||
425 cement | Electricity | t cement | 17.3 | 0.06 | ||||
525 cement | Electricity | t cement | 19.2 | 0.07 | ||||
625 cement | Electricity | t cement | 19.8 | 0.07 | ||||
Total | ||||||||
325 cement | 59 | 2.92 | ||||||
425 cement | 60 | 2.92 | ||||||
525 cement | 62 | 2.93 | ||||||
625 cement | 62 | 2.93 |
Assumptions: Ratio of "t of raw materials per t of clinker "is 1.77; ratio of "t of coal per ton of clinker" is 0.97; clinker to cement ratio in Portland cement is 0.95; additives to cement ratio in Portland cement is 0.05. |
Process | Energy carrier | Product unit | kWh/t product | GJ/t prduct | kWh/t clinker | GJ/t clinker | kWh/t cement | GJ/t cement |
---|---|---|---|---|---|---|---|---|
Raw materials preparation | Electricity | t raw meal | 12.05 | 0.04 | 21.3 | 0.08 | 13.9 | 0.05 |
Solid fuels preparation | Electricity | t coal | 10 | 0.04 | 0.97 | 0.92 | ||
Clinker making | Fuel | t clinker | 2.85 | 1.9 | ||||
Electricity | t clinker | 22.5 | 0.08 | 14.6 | 0.05 | |||
Additives preparation | Fuel | t additive | ||||||
Electricity | t additive | 7 | 0.03 | |||||
Finish grinding | ||||||||
325 cement | Electricity | t cement | 23 | 0.08 | ||||
425 cement | Electricity | t cement | 25 | 0.09 | ||||
525 cement | Electricity | t cement | 28 | 0.10 | ||||
625 cement | Electricity | t cement | 28 | 0.10 | ||||
Total | ||||||||
325 cement | 52 | 2.04 | ||||||
425 cement | 54 | 2.05 | ||||||
525 cement | 57 | 2.06 | ||||||
625 cement | na | na |
Assumptions: Ratio of "t of raw materials per t of clinker "is 1.77; ratio of "t of coal per ton of clinker" is 0.97; clinker to cement ratio in fly ash cement is 0.65; additives to cement ratio in fly ash cement is 0.35 (5% gypsum, 30% fly ash). |
Process | Energy carrier | Product unit | kWh/t product | GJ/t prduct | kWh/t clinker | GJ/t clinker | kWh/t cement | GJ/t cement |
---|---|---|---|---|---|---|---|---|
Raw materials preparation | Electricity | t raw meal | 12.05 | 0.04 | 21.33 | 0.08 | 7.5 | 0.03 |
Solid fuels preparation | Electricity | t coal | 10 | 0.04 | 0.97 | 0.34 | ||
Clinker making | Fuel | t clinker | 2.85 | 1.0 | ||||
Electricity | t clinker | 22.5 | 0.08 | 7.9 | 0.03 | |||
Additives preparation | Fuel | t additive | ||||||
Electricity | t additive | 25 | 0.09 | |||||
Finish grinding | ||||||||
325 cement | Electricity | t cement | 41 | 0.15 | ||||
425 cement | Electricity | t cement | 44 | 0.16 | ||||
525 cement | Electricity | t cement | 49 | 0.18 | ||||
625 cement | Electricity | t cement | 51 | 0.18 | ||||
Total | ||||||||
325 cement | 57 | 1.65 | ||||||
425 cement | 60 | 1.66 | ||||||
525 cement | 65 | 1.68 | ||||||
625 cement | na | na |
Assumptions: Ratio of "t of raw materials per t of clinker "is 1.77; ratio of "t of coal per ton of clinker" is 0.97; clinker to cement ratio in blast furnace slag cement is 0.35; additives to cement ratio in blast furnace slag cement is 0.65 (5% gypsum or anhydrites, 60% fly ash). |
Footnotes
Benchmark Footnotes:
EU-China Energy and Environment Programme (2009) Cement - A reference guide for the industry.
Worrell, E., Price, L., Neelis, M., Galitsky, C., Nan, Z. (2008) "World Best Practice Energy Intensity Values for Selected Industrial Sectors", Lawrence Berkeley National Laboratory. p.24 (Available here)
Globally, more than 3.3 billion tons of cement was produced in 2010. Graphs below show the global distribution of production and the shares of top 10 cement producing nations.
Globally, the cement sector is dominated by a small number of large companies. Largest cement companies, and their capacities and sales are also provided below.
Cement production is an energy intensive process, with energy costs representing 20-40% of production costs (IEA, 2007. p. 145).
Since 1990s, globally there has been a gradual reduction in the "clinker ratio" – the ratio of clinker to cement in the final product – which reflects in reduced specific energy consumption. China is believed to have the lowest clinker ratio in 2010, due to extensive use of granulated blast furnace slag, fly-ash, boiler bottom-ash and a variety of other substitutes.
The table below provides an overview of the availability of materials that can be used as clinker substitutes and their current consumption levels.
Clinker Substitute | Use in 2004 (Mt) | Availability (Mt) |
---|---|---|
Total blast furnace slag | n.a. | 180 – 220 |
Granulated blast furnace slag | 90 | 110 |
Fly ash | 222 | 445 |
Pozzolona | 50 | n.a |
General Industry Characteristics
Global Cement Consumption
2011 [1]
Name | Million tons |
2006 | 2568 |
2007 | 2763 |
2008 | 2830 |
2009 | 2998 |
2010 | 3294 |
TOTAL | 14453 |
2011 [1]
Global Cement Consumption by Region in 2010
2010 [2]
Name | % |
North Asia | 60 |
South Asia | 5 |
Australasia | 0.5 |
North America | 3 |
South America | 3 |
Central America | 0.5 |
Western Europe | 7 |
Eastern Europe | 3 |
Central Europe | 1 |
North & West Africa | 4 |
Central & South Africa | 1 |
Indian Sub-continent | 8 |
Middle East | 5 |
TOTAL | 101 |
2010 [2]
Top ten cement producing nations in 2010
2010 [3]
Name | Mt |
China | 1868 |
India | 216 |
USA | 65 |
Turkey | 62 |
Iran | 61 |
Brazil | 58 |
Vietnam | 55 |
Japan | 54 |
Russia | 50 |
Egypt | 48 |
TOTAL | 2537 |
2010 [3]
Capacities of leading cement companies
2010 [4]
Name | Mt |
Lafarge | 199 |
Holcim | 212 |
HeidelbergCement | 112 |
Cemex | 97 |
Italcementi | 81 |
TOTAL | 701 |
2010 [4]
Cement sales of leading companies (2010)
2010 [5]
Name | Mt |
Lafarge | 141 |
Holcim | 137 |
Heidelberg Cement | 78 |
Cemex | 66 |
Italcementi | 54 |
Buzzi Unicem | 27 |
TOTAL | 503 |
2010 [5]
Footnotes
[1] International Cement Review:http://www.cemnet.com/content/publications/gcr9_world_overview/player.html
[2] International Cement Review:http://www.cemnet.com/content/publications/gcr9_world_overview/player.html
[3] International Cement Review:http://www.cemnet.com/content/publications/gcr9_world_overview/player.html
[4] International Cement Review:http://www.cemnet.com/content/publications/gcr9_world_overview/player.html
[5] International Cement Review:http://www.cemnet.com/content/publications/gcr9_world_overview/player.html
There are numerous organizations working at global, regional, national levels with improving the resource productivity and reducing the environmental impact of cement manufactuing. Some of the major ones are listed below:
Original research for this section is performed by Lawrence Berkeley National Laboratory's China Energy Group.
Cement Organizations Global
Cement Organizations Asia-Pacific
Cement Organizations Australia
Cement Organizations Brazil
Cement Organizations China
Cement Organizations Europe
Cement Organizations European Union
Cement Organizations India
Cement Organizations United States
Cement Organizations Iran
Cement Organizations Japan
Cement Organizations South Korea
Cement Organizations Turkey
Programs Description:
There are a number of organizations working at global, regional, national levels with improving the resource productivity and reducing the environmental impact of cement manufacturing. Information on some of the major programs can be found below:
Cement Programs Global
Cement Programs Australia
Cement Programs China
Cement Programs European Union
Cement Programs India
Cement Programs Iran
Cement Programs Japan
Cement Programs Turkey
Cement Programs United States
Industrial energy efficiency can be greatly enhanced by effective management of the energy use of operations and processes. Experience shows that companies and sites with stronger energy management programs gain greater improvements in energy efficiency than those that lack procedures and management practices focused on continuous improvement of energy performance. An Energy Management Systems (EnMS), which is a collection of procedures and practices to ensure the systematic tracking, analysis and planning of energy use in industry, provides such a framework to manage energy and promote continuous improvement. They establish assessment, planning, and evaluation procedures which are critical for actually realizing and sustaining the potential energy efficiency gains of new technologies or operational changes.
There are a number of guidelines aimed at helping companies to establish an effective EnMS - including those from United States Environmental Protection Agency (US EPA) and the recent ISO 50000 series of the International Standards Organization.
Although they may differ in their details, these guidelines promote continuous improvement of energy efficiency through:
- Organizational practices and policies;
- Team development;
- Planning and evaluation;
- Tracking and measurement;
- Communication and employee engagement; and;
- Evaluation and corrective measures (US EPA, 2010)
While EnMSs can help organizations achieve greater savings through a focus on continuous improvement, they do not guarantee energy savings or carbon dioxide reductions alone. Combined with effective plant energy benchmarking and appropriate plant improvements, EnMSs can help achieve greater savings.
International Energy Agency (2009) Energy Technology Transitions for Industry. p. 78
International Energy Agency (2012) Tracking Clean Energy Progress. p.34