The U.S. Environmental Protection Agency’s (EPA) energy guide, Energy Efficiency Improvement and Cost Saving Opportunities for the U.S. Iron and Steel Industry, discusses energy efficiency practices and technologies that can be implemented in iron and steel manufacturing plants. This guide provides current real world examples of iron and steel plants saving energy and reducing cost and carbon dioxide emissions.
Electric Arc Furnace
Electric Arc Furnaces (EAFs) are a central part of the production route that is an alternative to the dominant BF-BOF route. EAFs are used to produce carbon steels and alloy steels primarily by recycling ferrous scrap. In an EAF scrap and/or manufactured iron units – such as DRI, pig iron, iron carbide – is melted and converted into high quality steel by using high-power electric arcs formed between a cathode and one (for DC) or three (for AC) anodes (Worrell et al., 2010. p. 14). Scrap is by far the he most important resource, accounting for about 80% of all electric arc furnace metal feedstock (IEA, 2007. p. 128).
The iron units are loaded in a basket together with limestone – for slag formation – and charged into the furnace. The main task of most modern EAFs is to convert the solid raw materials to liquid crude steel as fast as possible and then refine further in subsequent secondary steelmaking processes. Nevertheless, if time is available, almost any metallurgical operation may be performed during flat bath operation period (after melting), which is usually performed as a pre-treatment to the secondary steelmaking operations. Oxygen and coal powder injection are common treatment operations. (Worrell, et al., 2010. p. 14; Steeluniversity.org)
Total theoratical energy required to melt the scrap and to superheat it to the typical tap temperatures requires around 350 – 370 kWh/t-steel. This energy can be provided by the electric arc, from fossil fuel injection or oxidation of the scrap feedstock. In practice, the energy use is highly dependent on product mix, local material and energy costs and is unique to the specific furnace operation. Factors such as raw material composition, power input rates and operating practices – such as post-combustion, scrap preheating – can greatly influence the balance. Actual electricity use in EAFs are reported to range between 300 – 550 kWh/t, and in 1999 reached an average level of 425 kWh/t. Based on 2005 Figures, IEA estimated that reducing the average electricity consumption from 425 kWh to 350 kWh for every ton of steel produced in EAFs worldwide, 0.1 EJ of energy can be saved annually (IEA, 207. pp. 130-131).
Electric Arc FurnaceSchematic
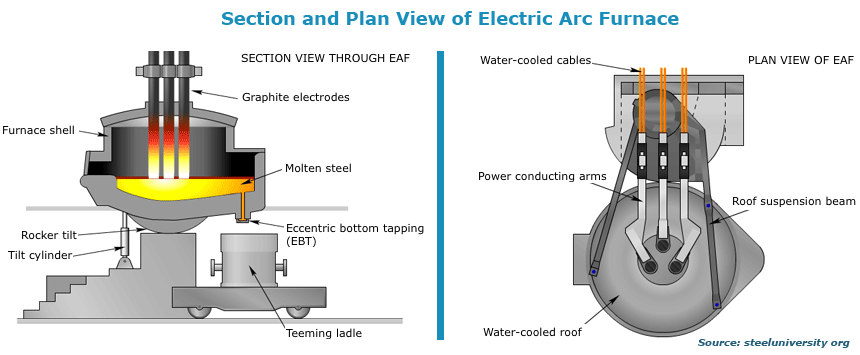
Electric Arc FurnaceTechnologies & Measures
Technology or Measure | Energy Savings Potential | CO2 Emission Reduction Potential Based on Literature | Costs | Development Status |
---|---|---|---|---|
Improved Process Control (Neural Networks) |
Electricity savings of 30 kWh/t-steel are estimated, and values may change based on scrap and furnace characteristics. (APP, 2010. p. 79) |
Emissions reduction potential of the technology is 17.6 kg CO2/t-steel (US EPA, 2010. p.11). |
Commercial | |
EAF Controls |
This technology results in 14% reduction in electricity consumption. Additionally a 6% reduction in natural gas consumption were achieved all together. |
Direct and indirect CO2 emissions reduction potential of the technology is 34 Kton/year. |
An Investment of €3.8 Million over two years aimed at energy savings was made. |
Commercial |
Oxyfuel Burners/Lancing |
2–3 kWh/t-steel of energy can be saved for every minute of heating time reduced; |
|
Retrofit capital cost for a 110t capacity EAF is $4.8/t. |
Commercial |
Flue Gas Monitoring and Control |
Electricity savings of 0.05GJ/t-steel are estimated by using this technology (US EPA, 2010. p. 11) . Chemical energy recovery rate from exhaust gases can be increased by 50% by adjusting oxygen injection levels for post-combustion based on real time CO and CO2 readings in flue gases, instead of using preset values (Worrell, et al., 2010. p. 90).
|
Emissions reduction potential of the technology is estimated to be 8.8 kgCO2/t-steel (US EPA, 2010. p. 11). |
Retrofit capital cost are estimated at $3.1/t-steel (US EPA, 2010. p. 11). The monitoring system installed in Mexico and the US resulted in yield improvements between 1% and 2%, decreased electrode consumption between 3.5% and 16%, increased productivityby 8%. |
Commercial |
Post Combustion Optimization in Steelmaking |
Energy requirement for BOF reduces by 30%. 50 to 100 kWh/tonne of steel electricity reduction in EAF is estimated. |
CO is combusted to produce CO2 and the energy. |
Commercial | |
Hot DRI/HBI Charging to EAF |
Charging hot DRI at temperatures up to 600 °C rather than cold DRI results in a melting energy reduction of 150 kWh/t-steel (>0.5 GJ/ton). |
Environmental emissions are lower due to energy savings. |
Commercial | |
Foamy Slag Practices |
The net energy savings are estimated at 6-8 kWh/t-steel (Worrell et al., 2010. p. 93). |
|
Retrofit capital cost is estimated at $15.6/t-steel (US EPA, 2010). |
Commercial |
Scrap Preheating |
Scrap preheating can save 0.016 to 0.2 GJ/t-steel. |
Commercial | ||
Bottom Stirring/Stirring Gas Injection |
Electricity savings can vary between 12 to 24 kWh, or 0.07 GJ, per ton of steel. |
Emissions saving potential of the technology is 11.7 kg CO2/t-steel. |
Retroftit capital cost is $0.94/t-steel. |
Commercial |
Shaft Furnace Scrap Preheating |
With single shaft furnace upto 77kWh/t-steel of electric energy can be saved. Finger shaft furnace allows savings up to 110 kWh/t-steel, which is approximately 25% of the electricity input (Worrell et al., 2010. p. 95). |
|
Retrofit costs were estimated to be $9.4/t-capacity for an existing 100 tonfurnace. Production cost savings may amount $6.7/t-steel. The payback time is estimated as one year. (US EPA, 2010. p.36) |
Commercial |
Tunnel Furnace Preheating – CONSTEEL Process |
Electricity savings are estimated to be 60 kWh/t for retrofits or 0.22GJ/t-steel. |
Emissions reduction of 35.5Kg CO2/tonne steel is achievable. |
Investment costs were estimated to be $3.2 million 500,000 t/y, or $7.8/t-steel. Annual costs savings were estimated to be $3.0/t-steel. The payback time is estimated as 1.3 years. (US EPA, 2010. p. 36) |
Commercial |
Direct Current (DC) Arc Furnace |
Net energy savings over older AC furnaces are estimated to be 0.32GJ/t-steel. Compared to new AC furnaces, the savings are limited to 0.036-0.072 GJ/t-steel (US EPA, 2010. p.35). |
Emissions reduction potential of the technology is 52.9 Kg CO2/t-steel (US EPA, 2010. p.11). |
The additional investment costs over that of an AC furnace are approximately $6.1/t capacity. The payback time is estimated as 0.7 years (US EPA, 2010. p.35). |
Commercial |
Waste Heat Recovery for EAF |
Approximately 130 kWh/t-s of energy can be recovered (efficiency 30%). |
If recovered energy is used for power generation with saturated steam, corresponding CO2 emission reduction will be 12,600 t/y; |
Research | |
Airtight EAF Process |
Energy savings are estimated to be around 110 kWh/t-steel (Worrell et al., 2010. p. 95) |
Significant emissions reduction can be expected due to reduction in energy consumption. |
Commercial | |
Adjustable Speed Drives (ASDs) |
Total fan energy consumption can be decreased by 67%. Electricity savings are estimated to be 16.5 kWh or 0.06 GJ per ton of steel. |
Decreased energy consumption will lower emissions. |
Retrofit capital costs are $2/tonne steel. The payback time is estimated as 2 to 3 years. |
Commercial |
Comelt |
Reduction of energy consumption of approximately 100 kWh/tonne is expected compared to the conventional EAF.
|
Reduced energy consumption will eventually result in reduced emissions. |
Maintenance costs would decrease due to a simpler plant design. |
Commercial |
Contiarc Furnace |
Energy losses are reduced by 220 kWh/t-steel as compared conventional furnace systems. Also electric power consumption reduces by 25 kWh/t-steel (0.091 GJ/t) due to reduced flue gas amount requiring cleaning. |
Waste gas and dust volumes are considerably reduced by the technology. |
|
Commercial |
Twin-Shell DC Arc Furnace |
Electricity savings are 0.068GJ/t-steel. |
Emissions reduction potential of the technology is 11.1KgCO2/t-steel. |
Retrofit capital cost is $9.4/t-steel over that of a single-shell furnace. The payback time is estimated as 3.5 years.. |
Commercial |
Post Combustion of EAF Flue Gas |
For a particular post-combustion system, electricity savings ranged from 6 to 11% depending on the operating conditions (Worrell et al., 2010. p. 93). |
Energy savings will result in reduced emissions. |
In a particular application tap-to-tap times were decreased by 3 to 11% depending on operating conditions (Worrell et al., 2010. p. 93). |
Commercial |
Engineered Refractories |
Savings of 11kWh/-steel are expected by applying this technology. |
Energy savings will result in reduced emissions. |
Commercial | |
Eccentric Bottom Tapping |
Electricity savings of 0.05GJ/t-steel are estimated by using this technology. |
Emissions reduction of 8.8 Kg CO2/t-steel are expected. |
Retrofit capital costs are $5.0/t-steel. |
Commercial |
ECOARC |
This furnace consumes 200 kWh/ton power at oxygen injection rate of 40Nm3/ton. |
Flexibility of scrap mixing reduces the costs for the process. Electrode consumption is as low as 0.8-1.0 kg/ton. |
Demonstration | |
Ultra High Power (UHP) Transformers |
Electricity savings are estimated to be 1.1 kWh/t-steel for every MW power increase. . |
|
To increase the operating voltage from 600V to 660V in one furnace and from 400V to 538V in another a $1.1 million investment was made (Worrell et al, 2010. p. 91). .Capital costs were estimated to be $3.9/ton ($4.3/tonne). The payback time is estimated as 5.2 years (US EPA, 2010. p. 33).
|
Commercial |
Used Tires for Insulation in EAF |
Electrical energy consumption to produce one tonne of billet was reduced from 424 kWh to 412 kWh. |
CO2 savings were equivalent to the removal of approximately 4,000 cars from the road. |
Using rubber tyres, steelmaking costs are 80% of what they were when using coking coal. |
Demonstration |
New-Scrap Based Steelmaking Process using Primary Energy |
About 32% reduction of primary energy Intensity for liquid steel production compared to the conventional EAF is expected by this technology. |
Depending on the CO2 emission of the electricity grid, the significant amount of CO2 emission will also be reduced. |
There will about 19% reduction in the energy cost per tonne of liquid steel produced. |
Demonstration |
Injection of Aluminium instead of Ferrosilicon for Stainless Steel Making in EAF |
Electrical energy demand was significantly decreased by approximately 10%. |
Reduction in emissions because CO is not let to oxidize rather it foams the slag. |
Cost decreases due to savings in alloying agents such as Cromium. |
Research |
Model Based Steel Temperature Measurement |
Energy savings are achieveable by the implementation of this technology. |
There will be related CO2 emission reduction. |
Evaluation of attainable savings will be performed on the basis of energy balance of whole process. |
Research |
Optimal Charge Calculation in EAF |
Energy-Optimal charging of scrap by using this technology. |
This technology is expected to bring savings of 5 – 10 % in scrap costs. |
Commercial | |
Holistic Quality Driven Production Control |
The technology reveals significant saving potential in terms of energy. |
Cost savings are obtained due to on-line monitoring of the amount of alloying agent. |
Demonstration | |
Dynamic Asymmetrical Control of AC EAF |
The melting rate was Improved by as much as 8 % by increasing the mean electric power Input and by shortening the power-off times. |
The economical mode of operation reduces the consumption of refractory gunning mixes by around 10 %. |
Commercial | |
Hydrogen and Nitrogen Control in Ladle and Casting Operations |
Better control results in energy savings by an estimated 400 million kilowatt hours (kWh) per year. |
CO2 emissions decreases. |
Estimated annual savings are $20 million when technology is in widespread commercial use. |
Research |
Modification of Side Wall Water Cooled Panels and Water Header |
This technique increases furnace capacity by 18-20 tonnes. Power consumption was reduced from 800 kWh to 620 kWh/t-steel. |
Annual savings of Rs. 864 000 000 were obtained. |
Commercial | |
Development of a process to continuously melt, refine and cast high quality steel |
A total of 10% energy savings will occur by reducing the energy needed for auxiliary operations. Savings of 20 kWhr/t in auxiliary energy are reported. |
Capital cost for the equipment is $35 million for a 1,000,000 tpy facility. |
Demonstration |
Electric Arc Furnace Publications
Energy Efficiency Improvement and Cost Saving Opportunities for the U.S. Iron and Steel Industry
Page Number:
Available and Emerging Technologies for Reducing Greenhouse Gas Emissions from the Iron and Steel Industry
Page Number:
The State–of-the-Art Clean Technologies (SOACT) for Steelmaking Handbook
Date:
Source:
Format:
Type:
The State–of-the-Art Clean Technologies (SOACT) for Steelmaking Handbook is developed as part of the Asia-Pacific Partnership on Clean Development and Climate program and seeks to catalog the best available technologies and practices to save energy and reduce environmental impacts in the steel industry. Its purpose is to share information about commercialized or emerging technologies and practices that are currently available to increase energy efficiency and environmental performance.
Page Number:
Global Warming Countermeasures: Japanese Technologies for Energy Savings / GHG Emissions Reduction
Date:
Source:
Format:
Type:
This revised 2008 version of the publication from New Energy and Industrial Technology Development of Japan includes information on innovative Japanese technologies for energy efficiency and for the reduction of CO2 emissions.