Circular Economy
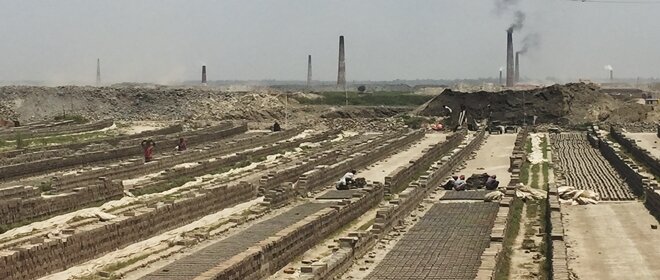
Promoting Symbiotic Win-Win Models of Waste Recycle
The underlying objective behind some of the projects implemented by the IIPI is to promote energy efficiency, resource conservation and GHG mitigation through use of cleaner technologies, processes, raw materials and approaches. The choice of sectors and technologies in these projects have been such that they promote symbiotic models of waste recycle and reuse between different industrial sectors creating win-win situation for a range of stakeholders. These interventions have resulted in substantial energy, material and water saving along with waste minimisation, with industry benefitting by way of improved resource productivity, product quality and higher profit; workers and society benefitting throughreduced social and health impacts such as improved workplace environment, safety at workplace, reduced respiratory diseases, stable employment; and Government on account of reduced environmental and climate change impacts.An overview of some of these projects and the ways in which they promote industrial symbiosis are as follows:
Promoting Resource Efficient Brick Technology in Bangladesh through a South-South cooperation approach
Brick sector contributes to 1% of Bangladesh’s GDP and employs more than 1 million people. However, Bangladesh’s brick sector is characterized by outdated technologies with low energy efficiency, high emissions and dominance of single raw material (clay) and product (solid clay brick). Bangladesh currently produces around 17 billion bricks per year, consuming around 45 million tonnes of agricultural soil, which is equivalent to around 2,600 hectares of agricultural land. With the prevailing growth rate of close to 10 % per annum, brick manufacture will threaten the food security of the country in the near future. Apart from clay, brick kilns burn nearly 3.5 million tons of coal and another 1.9 million tons of wood annually. Given these concerns, Bangladesh government has recently banned the Fixed Chimney Kilns (FCKs) technology and mandated its gradual phase out to other more efficient technologies. However, adoption of gas-based cleaner and efficient technologies in brick sector is hampered by declining Gas reserves in the country.
It is in this context that IIPI is promoting an innovative FaL-G Brick (Fly ash- Lime- Gypsum) technology in Bangladesh brick sector that has been invented and patented in India. This new method of brick making has the potential to completely eliminate carbon emissions from brick-making as it does not require coal or other energy sources to manufacture brick. Another significant benefit of the new technology is that unlike clay bricks that use valuable agricultural top soil as raw material, it uses fly ash, an unwanted residue from coal burning (mainly from coal-fired power plants). Bangladesh government is commissioning three new large coal based super critical thermal power plants to address the energy security concerns. It is estimated that 1.3 million cubic feet of fly ash will be generated from these power plants alone, and is estimated to reach an alarming level of 9.5 million cubic feet by 2018.The fly ash currently generated is dumped on large parcels of land, damaging both the environment and the health of populations around power plants.Putting fly ash to productive use thus reduces water, air, and soil pollution and respiratory problems of the populations living near thermal power plants. Fly ash is mixed with two other ingredients available as industrial by-products: Lime from the acetylene industry and Gypsum from chemical plants.
A further advantage is that fly ash bricks can be produced in a variety of strengths and sizes. This means that apart from their conventional use in building walls etc. fly ash bricks can also be used for the construction of a variety of infrastructure projects such as roads and pavements, dams and bridges. In India, 18000 FaL-G brick units have already been established and IIPI is now promoting this technology along with enabling policy measure in partnership with Bangladesh Department of Environment, Bangladesh Bick Manufacturer Owner Association and Infrastructure Development Company Limited (IDCOL), which is the state financial institution, wherein the inventors of the FaL-G technology have agreed to disseminate it with IIP without any technology transfer fee. In the long run (as is highlighted in the next section), it is also planned to make FaL-G bricks in Bangladesh by using textile sludge as a raw material. If this second phase of the program is successful, it would not only help in bringing down the cost of FaL-G manufacture but also solve one of the pressing environmental problems being faced by the Bangladesh, i.e., effective management and disposal of textile sludge.
Promoting Zero Liquid Discharge in the Textile Sector
Textile industry in Bangladesh contributes to 15% of its GDP, 80% of its exports and provides direct employment to 4 million people. It also stands second in terms of global exports after China. Although the textile sector is the backbone of Bangladesh’s economy, it is faced with numerous challenges due to its’ high resource (energy, water and chemical use) footprint and its consequent environmental impacts. The Bangladesh textile industry uses 2-3 times more water than the global benchmark. Besides high water footprint, the textile industry also faces the problem of managing the effluent discharge. Direct discharge of untreated effluent to the river stream has serious health and environmental impacts. Textile industry in Bangladesh also uses coagulants and chemicals to treat the effluent produced during the processing of textile. As a result, large amount of sludge is generates from primary and secondary clarifiers. The sludge collected from clarifiers is dried in sludge drying beds and is sent to landfills.Realising the scale of these issue and the urgent need for addressing it, Bangladesh government has recently issued the Zero Liquid Discharge (ZLD) Regulation mandating all textile mills to have compulsory installation of zero liquid discharge effluent treatment plant (ZLD-ETP) systems. However its practical application is fraught with technical and financial issues. IIP is supporting the Bangladesh Textile sector in implementing viable models of ZLD.
IIP is helping Bangladesh textile industry to shift from the approach of ZLD to Zero Waste Discharge. This is being supported by promoting the use of textile sludge as (i) raw material and (ii) alternate fuel in other industries. The FaL-G brick making technology being promoted by IIPI in brick sector of Bangladesh allow the use of textile sludge as a raw material in brick manufacture. Working with the textile and brick sectors simultaneously provides IIP an opportunity to demonstrate resource efficient circular economy win-win.Besides this, IIP has been working very closely with the cement industry in India for promoting the use of waste as alternative fuel in cement manufacture of which many cement plants use textile sludge as fuel, for e.g. Aditya Birla Cement, Chittorgarh (Rajasthan, India) unit has been co-incinerating ETP sludge of about 1000 tonnes per month from textile mills from Bhilwara Industrial Area. IIP is promoting similar concept in Bangladesh textile industry in partnership with Department for Environmental, Ministry of Environment and Bangladesh Garment Manufacturers and Exporters Association (BGMEA).
Promoting the use of Alternative Fuel and Raw Material (AFR) in Cement Industry
While the Indian cement industry has made significant achievements in terms of improvement in energy efficiency & productivity, AFR usage still remains a major area of concern. At present, the extent of fossil fuel substitution, as defined by TSR (Thermal Substitution Rate) of the Indian cement industry is below 1%, while in some developed countries, it is around 60%. In this context, IIP India launched a multi stakeholderinitiative to draw up an action plan for promoting increased use of AFR in cement kilns. IIP is working closely with the Cement Manufacturers Association (CMA) for implementation of this action plan for (i) five wastes viz. municipal solid waste, hazardous wastes, used tyres, plastic waste, the disposal of which are becoming an issue of increasing concern and, (ii) use of steel slag and fly ash as blending material, which can reduce the limestone requirement per tonne of cement and hence the energy requirement, thus saving on fossil fuels and mitigating both fuel as well as process related carbon emissions.
In order to identify and resolve the regulatory and policy issues for promoting use of AFR, IIP created a Forum of Regulators with high level representation from State Pollution Control Boards of major cement producing states in India. The Forum of Regulators reviewed the provisions of existing policy and regulatory guidelines and came out with a series of recommendations that were developed as five White papers. The Central Pollution Control Board (CPCB) appreciated the work done by the Forum and created a ‘National Task Force on Co-processing’, to take the recommendations of the Forum forward. This Task Force has now been created and convened by CPCB. The White paper compendium developed by IIP was released and presented at the first meeting of the National Task Force (NTF) and became the starting point of deliberations of the Task Force.
Promoting use of Spent Pot Liners of Aluminium Industry as fuel in Cement Industry- Catalysing change through the Knowledge Exchange Platform
Aluminium industry is looking at effective ways for disposal of Spent Pot Liners (SPL). Although SPL has high calorific value and can be used as an alternative fuel in cement industry, it is not being adopted because of presence of cyanide (which is a hazardous chemical) as a result of which it cannot be used directly by the cement industry. The current practice is to dispose it in secured landfill, but it may have long term impacts on ground water and soil pollution. There are international technologies available that can help in segregating cyanide from SPL after which it can be used effectively as a fuel in cement industry. IIPI (in partnership with BEE) through its Knowledge Exchange Platform (KEP) initiative is introducing these technologiesin Aluminium and cement sectors. Besides technology issues there are other policy and institutional barriers that are inhibiting the effective waste recycle between the two sectors. IIP through the ‘Policy Forum’ created under KEP initiative is working with the two sectors along with BEE and other concerned ministries to work out solutions and implement policy reforms.