Clinker Making
Clinker is produced by sintering limestone (calcium carbonate) and clay (alumino-silicate) at elevated temperatures. The production of clinker involves the feeding of the raw meal into the kiln, where first the calcination of calcium carbonate takes place and then the resulting calcium oxide is burned at high temperatures together with silica, alumina and ferrous oxide to form clinker.
Clinker making is responsible for 90% of the total energy consumption in cement plants. In modern plants, hot exhaust gases are used for pre-calcination, for pre-heating the raw meal and may also be used for additional energy recovery, thereby helping to reduce energy consumption.
Clinker MakingSchematic
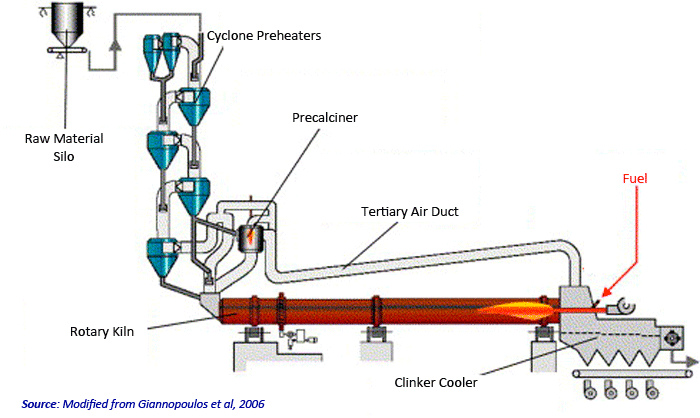
Clinker MakingTechnologies & Measures
Technology or Measure | Energy Savings Potential | CO2 Emission Reduction Potential Based on Literature | Costs | Development Status |
---|---|---|---|---|
Cement Suspension Preheater Calcining Technology with High Solid-Gas Ratio |
|
N/A |
|
Commercial |
Waste Heat Recovery for Power Generation |
Typically, 8–22 kWh/t-clinker can be produced without changes to kiln operation. Generation up 45 kWh/t clinker is possible by modifying kiln operations (e.g. less cyclone stages or by-passing upper stage(s) (CSI/ECRA, 2009. p. 31)
|
|
For a plant with 2 millon t-clinker/y capacity, installation costs are estimated to be between € 15-25 million. Operational costs are estimated to decrease by €0.3–1.2/t-clinker (CSI/ECRA, 2009. p.32).
|
Commercial |
Process Control and Optimization in Clinker Making |
Savings vary between 2.5 to 10% and typical values are estimated to be 2.5 to 5%.
|
The costs of process control optimization measures/techniques vary widely and can be up to $6.8 million [1€=$1.35 US]
|
Commercial | |
Combustion System Improvements |
Specific fuel savings up to 8% have been realised in plants using Gyro-Therm technology. Another technique developed in the UK for flame control resulted in fuel savings of 2 to 10% depending on the kiln type. |
The payback times for Gyro-Therm technology is expected to be less than one year. Costs are estimated to be around $1.0/annual ton clinker capacity, with estimated payback periods of 2-3 years. |
Commercial | |
Dry Kilns with Multistage Pre-heaters and Pre-calcination |
Fuel savings up to 3.0 GJ/t-clinker can be realized. Electricity consumption can increase by around 9 kWh/ton clinker. In a case in UK, two wet process kilns with a total heat requirement of 5.65 GJ/t-clinker were replaced with a single pre-heater/pre-calciner kiln resulting in energy saving of 36% (down to 3.5 GJ/t-clinker). |
Emission reductions are estimated to be:
|
Commercial | |
Conversion of Long Dry Kilns to Preheater/Precalciner Kilns |
Up to 1.4 GJ/t-clinker can be saved. |
For every ton of clinker, following amounts of CO2 reductions are estimated: 132.4 kg in Chinese context;
|
Upgrading costs are reported to be between US $8.6 to $29 per annual ton of clinker capacity. |
Commercial |
Kiln Shell Heat Loss Reduction |
Fuel consumption is estimated be reduced by around 0.12 to 0.4 GJ/t of clinker. |
|
Switching to higher quality refractories may cost around US $0.25/annual tonne clinker capacity. Estimated payback period is approximately 1 years. |
Commercial |
Addition of Pre-Calcination to Kilns with Preheaters |
In an Italian plant, the conversion reduced specific fuel consumption from 3.6 to 3.1-3.2 GJ/t clinker, resulting in savings of 11 to 14%, and enabled a capacity increase of 80 to 100% (from 1100 tpd to 2000 to 2200 tpd). |
|
Investments in the range of US $9.4-28 per annual ton clinker may be required. Payback times are usually less than 5 years.
|
Commercial |
Replacing Vertical Shaft Kilns |
Savings up to 2.4 GJ/t clinker can be obtained.
|
|
Costs of such conversions can be between US $28-41 per annual ton of clinker production. |
Commercial |
Low Pressure Drop Cyclones for Suspension Preheaters |
Power savings in the range of 0.7-4.4 kWh/t clinker depending upon feasibility of cyclone modification and fan efficiency.
|
|
The cost of a low-pressure drop cyclone system is assumed to be US $3 per annual ton clinker capacity. Installation of the cyclones can be expensive, since it may often entail the rebuilding or the modification of the preheater tower, and the costs are very site specific. |
Commercial |
Additional Preheater Cyclone Stages |
Moving from 4 stage to 5 stage, or from 5 stage to 6 stage can reduce the specific heat energy consumption between 0.08 to 0.1 GJ/t clinker
|
|
Commercial | |
High Efficiency Fans for Preheaters |
0.7 kWh of electricity can be saved for each ton of clinker produced.
|
CO2 emissions can be reduced by:
|
Capital costs of US $0.01 per annual ton of clinker capacity are reported. |
Commercial |
Bucket Elevators for Kiln Feed |
Following savings in electricity consumption are reported in literature:
|
Following cost informatin is provided in the literature:
US-EPA reports a US $0.17/ton-portland cement reduction in operating costs. |
Commercial | |
Fluidized Bed Advanced Cement Kiln System |
Thermal energy use can be decreased by around 0.4 GJ/t-clinker (NEDO, 2006), while the electricity consumption increases by around 9 kWh/t-clinker (ECRA, 2009) 20% more heat can be recovered in the cooling system, as compared to conventional methods (APP, 2009) |
CO2 reductions in the range of 10% can be realized (NEDO, 2006). |
Demonstration | |
Efficient kiln drives |
0.5 – 1% reduction in electricity use of the kiln drive can be achieved by replacing a DC motor with AC motor. Using high-efficiency motors to replace older motors, or instead of re-winding old motors, may reduce power costs by 2 to 8%. Electricity savings are 0.55-3.9 kWh/t clinker |
The capital cost for single pinion drive with an air clutch and a synchronous motor is around 6% higher than standard kiln drive. |
Commercial | |
Improved Burnability Using Mineralizers |
Based on the modelling results, thermal energy consumption can be reduced by between 0.05 to 018 GJ/t clinker. |
CO2 emissions can be reduced by 4 to 16 kg per ton of clinker |
Additional costs of mineralizers has to be considered and may outweigh the fuel cost savings. Espeically CaF2, which is commonly used, is an expensive material. Use mineral wastes containing flourides can be economically viable, however, such materials have a limited availability. |
Commercial |
Alkali Bleed (alkali by-pass) Systems | Commercial | |||
Oxygen enrichment technology |
Thermal energy use can be decreased by 0.1 - 0.2 GJ/t clinker but electricity use increases by 10 - 35 kWh/t clinker |
While this technology may reduce direct CO2 emissions by 10 to 20 kg per ton of clinker due to reduced fuel consumption, the indirect emissions are estimated to rise by 15 to 25 kg/t clinker due to increased electricity use. |
Demonstration | |
Using modern multi-channel burners |
Depending on the secondary air temperature, reduction of the primary air ratio by 5-10% will lead to a fuel energy saving of 0.05-0.08 GJ/t-clinker at conventional kilns and about half of this at precalciner kilns. The electrical energy demand will remain almost unchanged as the higher consumption for control fittings and air delivery channels can be offset by the reduction of the primary air.
|
|
|
Commercial |
Stabilization of Kiln Coating |
Radiation heat losses will be reduced leading to energy savings. |
Commercial | ||
Indirect firing |
Assuming a reduction of excess air between 20% and 30%, indirect firing may lead to fuel savings of 0.015 -0.022 GJ/t clinker. The advantages of improved combustion conditions will lead to a longer lifetime of the kiln refractories and reduced Nox emissions. These co-benefits may result in larger cost savings than the energy savings alone. |
US $5 million for an annual production capacity of 680,000 ton clinker, or US $7.4/t annual clinker capacity. |
Commercial |