This introductory movie is the first part of a set of nine training movies providing specific guidance on how to use the Assessment to Action (A2A) Toolkit, which is a free suite of resources on energy management and technology best practices created for ammonia companies.
Ammonia
The chemical and petrochemical sector is the largest industrial energy consumer. Ammonia production is responsible for about 17% of the energy consumed in this sector. In 2004, the ammonia manufacturing industry consumed 5.6 EJ of fossil fuels, of which 2.7 EJ was for energy and 2.9 EJ for feedstock use.1 Although the energy use per tonne of ammonia has decreased by 30% over the last thirty years, adopting best available technologies (BAT) worldwide can further reduce energy use by 20-25%1, 2 and decrease greenhouse gas emissions by 30%.2
Ammonia is produced by the reaction of hydrogen and nitrogen, dubbed the "Haber-Bosch process". Depending on the feedstock that is being used, the two main hydrogen production processes used in ammonia production are:
- Steam/air reforming process. Feedstocks include natural gas or other light carbon fuels such as natural gas liquids, liquefied petroleum gas and naphtha.
- Partial oxidation process. Feedstocks include heavy oils and coal.
The type of feedstock used to produce ammonia plays a significant role in the amount of energy used and CO2 produced. The production of ammonia from natural gas is the least energy intensive, and production with coal, which is predominantly used in China, generally has the highest energy consumption and CO2 emissions. Globally about 72 percent of ammonia is produced from natural gas using the steam reforming process.4 Coal as feedstock for hydrogen production in ammonia plants is predominantly used in China and is generally characterized by high energy consumption and CO2 emissions.3 Switching from coal or oil-based ammonia production to natural gas-based production will result in major energy and greenhouse gas emission savings. Other feedstocks for hydrogen production in ammonia plants include heavy fuel oil, naphtha, coke oven gas and refinery gas. On average, about one-third of the greenhouse gas emissions produced in natural gas-based production comes from fuel combustion and two-thirds from the use of natural gas used as feedstock. In coal-based ammonia plants, 25 percent of greenhouse gas emissions come from fuel burning and 75 percent from the use of coal as feedstock.3
Ammonia Schematic
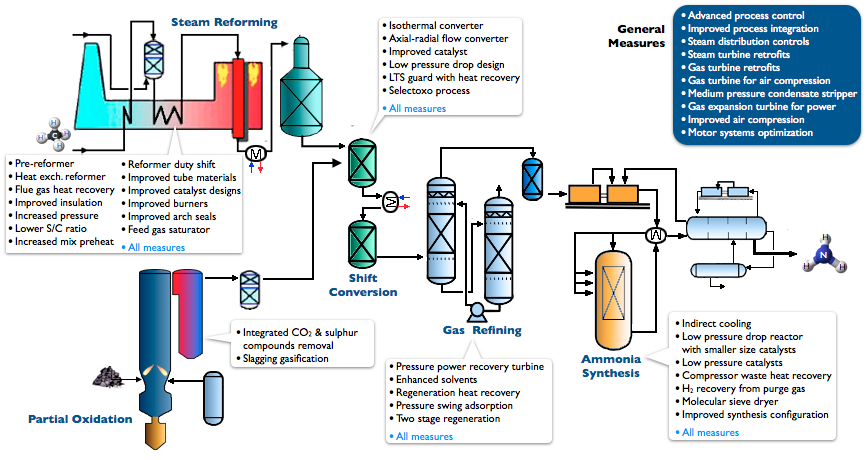
Ammonia Processes
Cross-Sectoral Systems
Selected Ammonia Technologies & Measures
For a wider list of technologies & measures, please follow the links under processes above.
Products
- Ammonia
Ammonia Videos
Using the Assessment to Action (A2A) Tool
Ammonia Reference Documents
Reference Document on Best Available Techniques for the Manufacture of Large Volume Inorganic Chemicals - Ammonia, Acids and Fertilisers
Date:
Format:
Type:
Prepared by the Institute for Prospective Technical Studies of European Commision, this document provides detalied information on Best Available Technologies applicable to Ammonia production – as well as on the production of Acids and Fertilizers.
Ammonia Guidelines
Best Available Techniques for Pollution Prevention and Control in the European Fertilizer Industry - Production of Ammonia
Date:
Format:
Type:
Produced by the European Fertilizer Manufacturers' Association, this guidance documents gives information on Best Avaiable Technologies applicable to ammonia production.
Ammonia Case Studies
Energy Efficiency Opportunities - Case Study Incitec Pivot Limited (IPL) - Gibson Island
This case study, prepared by the Australian Government's Department of Resources, Energy and Tourism, looks at the assessment approach adopted by a major chemical manufacturer participating In The Energy Efficiency Opportunities (EEO) Program.
Ammonia Tools
Assessment to Action (A2A) Toolkit
Developed by IIP, in collaboration with energy expertsat ICF Marbek, members of the IFA and experts in China, the A2A (Assessment to Action) Toolkit is a free suite of resources on energy management and technology best practices created for ammonia companies. The A2A Toolkit provides a first-order, high-level assessment to identify and prioritize energy efficiency opportunities. It does so by drawing on various assessment modules on technical best practices, management best practices (based on ISO 50001 standard) and productivity improvements.
In ammonia production, the type of feedstock used plays a significant role in the amount of energy that is consumed and CO2 produced. The type of technology used is another key factor. The steam reforming of natural gas produces on average 2.1 tCO2/t NH3, while in partial oxidation the emissions are about 3.3 tCO2/t NH3 when fuel oil is used and 4.6 tCO2/t NH3 when coal is used to produce hydrogen.a, b This is followed by the type of technology employed. According to a benchmarking study conducted by the International Fertilizer Industry Association (IFA) in 2008, the average net energy efficiency in 93 ammonia plants was 36.6 GJ/t NH3. The energy efficiency of the best performers (top quartile) ranged between 28 and 33 GJ/t NH3. The Best Practice Technology (BPT) energy use for the top quartile of natural gas-based producers was 32 GJ/t NH3. This indicates that a wide adoption of BPTs can decrease energy use and greenhouse gas emissions by approximately 10 percent. The energy use for Best Available Technology (BAT) is 28 t NH3. Worldwide implementation of BATs would result in 25 percent energy savings and a reduction in greenhouse gas emissions of about 30 percent. 2 Table 1 and 2 below provide information on best practice energy use, BAT energy use and CO2 emission values.
The energy use for ammonia production varies across the world. This is mainly due to the combination of the type of feedstock and technology used in different countries. Considering both the feedstock composition and the technology level, it is estimated that China is 35 percent less efficient than Western Europe, Saudi Arabia and Taiwan. Ammonia production in Japan and Korea is estimated to be 5 percent more efficient than Western Europe. Compared to Western Europe, ammonia production in North America and India is estimated to be 5 percent and 15 percent less energy efficient respectively.5 Table 3 shows the estimated specific energy consumption for ammonia production in 2010 in different regions.
Further information on benchmarks on critical process parameters affecting energy efficiency in Indian plants is available here.
Ammonia Benchmarks
Process |
Final energy (GJ/tonne NH3) |
Primary energy (GJ/tonne NH3) |
Source |
||||||
---|---|---|---|---|---|---|---|---|---|
Electricity |
Feedstock |
Fuel |
Steam |
Electricity |
Feedstock |
Fuel |
Steam |
||
Ammonia from natural gas |
0.29 |
20.67 |
10.93 |
-3.87 |
0.74 |
20.67 |
10.93 |
-4.3 |
Schyns, 2006 |
Ammonia from coal |
3.7 |
20.67 |
17.33 |
-1.3 |
9.25 |
20.67 |
17.33 |
-1.44 |
AIChE, 2008; IFA, 2009a |
Ammonia from oil |
0.7 |
20.67 |
16.13 |
-1.5 |
0.74 |
20.67 |
16.13 |
-1.67 |
IFA, 2009a |
Note: Ammonia is most commonly produced from natural gas and therefore the BPT values for this feedstock are used for all countries, except for India and China, where other types of feedstock are widely used. The best practice final energy use for oil-based ammonia production is assumed to be 30% higher compared to natural gas-based ammonia production (AIChE, 2008; IFA, 2009a). The best practice final energy use for coal-based ammonia production is assumed to be 50% higher than natural gas-based ammonia production (IFA, 2009a).
Energy Source |
Process |
Energy GJ/tonne NH3 |
CO2 emissions t/tonne NH3 |
GHG index |
---|---|---|---|---|
Natural Gas |
Steam reforming |
28 |
1.6 |
100 |
Naphtha |
Steam reforming |
35 |
2.5 |
153 |
Heavy Fuel Oil |
Partial oxidation |
38 |
3.0 |
188 |
Coal |
Partial oxidation |
42 |
3.8 |
238 |
Region | Production Mt NH3/yc |
Share of feedtsock type (%) | Specific Energy Use (GJ/t NH3) |
Total Fuel Use |
CO2 Emissionsd (Mt CO2/y) |
|||||||
---|---|---|---|---|---|---|---|---|---|---|---|---|
Natural Gas | Oil | Nahta | Coal | Natural Gas | Oil | Naphta | Coal | Average | ||||
Western Europe | 11.0 | 90 | 10 | 35.0 | 42.5e | 35.8 | 393 | 23.0 | ||||
North America | 14.7 | 100 | 37.9 | 37.9 | 557 | 31.3 | ||||||
CIS | 21.0 | 100 | 39.9 | 39.9 | 838 | 47.0 | ||||||
Central Europe | 5.2 | 95 | 5 | 43.6 | 42.5e | 43.5 | 226 | 12.9 | ||||
China | 49.7 | 24f | 1f | 0 | 75f | 34 | 42.0 | 54.0 | 49.1 | 2440 | 220.1 | |
India | 14.0 | 80g | 10g | 9g | 36.5 | 50.0 | 39.0 | 37.7 | 528 | 31.9 | ||
Other Asia | 10.9 | 100 | 37.0 | 37.0 | 403 | 22.6 | ||||||
Latin America | 9.9 | 100 | 36.0 | 36.0 | 356 | 20.0 | ||||||
Africa | 6.3 | 100 | 36.0 | 36.0 | 227 | 12.7 | ||||||
Middle East | 12.7 | 100 | 36.0 | 36.0 | 457 | 25.6 | ||||||
Oceania | 1.9 | 100 | 36.0 | 36.0 | 68 | 3.8 | ||||||
World | 157.3 | 72.4 | 4.3 | 0.8 | 22.4 | 41.3 | 6495 | 451 |
Footnotes
Benchmark Footnotes:
IPCC (2006). 2006 IPCC Guidelines for National Greenhouse Gas Inventories. Chapter 3 – Chemical Industry Emissions (Available here).
Zhou, W., Zhu, B., Qiang, L., Ma, T., Hu., S., Griffy-Brown, C. (2010). CO2 emissions and mitigation potential in China’s ammonia industry. Energy Policy 38, pp.3701-3709.
International Fertilizers Association (IFA) (2012). Production and Trade Statistics. Paris, France.
The values refer to the amount of CO2 produced in ammonia production and do not account for possible use of CO2 in other industrial processes (e.g. urea production). CO2 emissions are calculated based on carbon content of 15.3 kg/GJ for natural gas, 21 kg/GJ for fuel oil, 19.6 kg/GJ for fuel oil, and 26.5 kg/GJ for coal (IPCC, 2006 p.3.15; Zhou et al., 2010; U.S. EPA, 2012 p.32).
Average value for European plants (IPCC, 2006 p.3.15)
China Chemical Energy Conservation Technology Association –CCECT (2011) China Petrochemical Energy Report.
The Fertilizer Association of India (2012).
International Energy Agency (IEA), 2007. Tracking Industrial Energy Efficiency and CO2 Emissions. p.85
About 80 percent of ammonia produced is used as fertilizer and is applied either directly or converted to solid fertilizers before application (e.g. urea, ammonia nitrate). The remaining 20 percent is used in a variety of industrial applications, such as in the manufacture of plastics, fibers, explosives, amines, amides and other organic nitrogen compounds (IPTS/EC, 2007 p.35). Nitric acid, urea and sodium cyanide are the main products derived from ammonia. The fertilizer industry is a major energy consumer, responsible for about 2-3 percent of global energy consumption (IPTS/EC, 2007 p.3). Production of ammonia accounts for about 80-90 percent of the energy used in the manufacture of fertilizers (IEA, 2007 p.60).
Between 2000 and 2011, global ammonia production increased by 25 percent, from 131 million tonnes ammonia to 164 million tonnes. This represents an annual increase of about 2 percent on average (USGS, 2012). Over the past 15 years the largest (absolute) growth has been in China, where overall production increased by 65 percent. Trinidad and Tobago, India and Russia have also experienced large (absolute) growths in ammonia production over the past 15 years. In the United States, the production capacity of ammonia significantly decreased over this period by about 30 percent. Figure 1 shows the historical ammonia production trends since 1996.
Figure 1: Historical ammonia production trends (USGS, 2012)
Natural gas, naphta, heavy fuel oil, coal, coke oven gas and refinery gas can be used as feedstock in ammonia production. Globally, 72 percent of ammonia is produced using steam reforming of natural gas (IEA, 2012 p.329) and is the least energy intensive option. Coal is predominantly used in China and is generally characterized by high energy intensities. The table below provides the estimated distribution of feedstock use in selected countries.
Worlda |
Japan |
Benelux |
Germany |
USA |
Brazil |
Canada |
China |
France |
India |
Italy |
Korea |
Saudi Arabia |
Taiwan |
|
---|---|---|---|---|---|---|---|---|---|---|---|---|---|---|
Natural gas |
72.4% |
100% |
100% |
67% |
97% |
100% |
100% |
24%b |
69% |
80%c |
90% |
N/A |
100% |
100% |
Naphtha |
0.8% |
|
|
|
|
|
|
0% |
|
9%c |
|
|
|
|
Oil |
4.3% |
N/A |
N/A |
33% |
3% |
N/A |
N/A |
1%b |
31% |
10%c |
10% |
100% |
N/A |
N/A |
Coal |
22.4% |
N/A |
N/A |
N/A |
N/A |
N/A |
N/A |
75%b |
N/A |
N/A |
N/A |
N/A |
N/A |
N/A |
a: Based on Table 3 under benchmarks section; b: China Chemical Energy Conservation Technology Association (CCECT), 2011; c: Fertilizer Association of India (2013)
Developments in Energy Use in Ammonia Plants
Increasing feedstock and energy prices in combination with increased competitiveness have forced many ammonia producers to revamp or modernize older and inefficient plants. Most of the revamp projects that have taken place were combined with a moderate increase in capacity (IPTS/EC, 2007 p.35).
The first single-train ammonia plant had an energy use of about 45 GJ/t NH3 (Ullmann’s, 2011 p.229). An energy efficient ammonia plant is characterized by an energy use of less than 29 GJ/t NH3. Significant developments that contributed to the major reduction in energy use were improvements in the steam reforming section, such as heat recovery from the primary reformer flue-gases, the installation of a pre-reformer, increased reformer operating pressure, lower steam to carbon ratios and shifting the primary reformer duty to the secondary reformer. Improvements have also taken place in other aspects of ammonia manufacture. For example, in shift conversion with the use of improved catalysts, in CO2 removal with the use of new solvents, and in ammonia synthesis with the use of improved catalysts and improved reactor designs. More developments consist of higher efficiency turbines and compressors, improved process control and process optimization.
The applicability rate of energy efficiency improving technologies for different countries is hard to determine as it strongly depends on the level of technology currently adopted. An estimate of the share of plants to which several revamps can be applied in the European Union, the United States and in India are given in the table below (Rafiqul et al., 2005).
Type of Energy Efficiency Improvement | Applicability Rate (share of plants in percentage) | ||
---|---|---|---|
Euoropean Union | United States | India | |
Reforming (large improvements) | 10 | 15 | 10 |
Reforming (moderate improvements) | 20 | 25 | 20 |
CO2 removal section | 30 | 30 | 30 |
Low pressure ammonia synthesis | 90 | 90 | 90 |
Hydrogen recovery | 0 | 10 | 10 |
Improved process control | 30 | 50 | 30 |
Proces Integration | 10 | 25 | 20 |
The energy efficiency of ammonia production depends on the feedstock type that is being used and the plant production scale (IEA, 2007 p.84). Coal-based ammonia production in China takes place primarily in small-scale plants (90%). The remaining 10 percent is produced in medium-scale plants. The energy intensity of these medium-scale coal-based plants is about 55 GJ/t NH3, while small-scale coal-based plants consume about 53 GJ/t NH3. It is not clear why small-scale plants consume slightly less energy than medium-scale ones. In China, a shift to natural gas is not foreseeable due to recent major investments in coal-based processing plants (IEA, 2009b p.19). On the contrary, higher future natural gas prices may result in a wider uptake of coal-based processes (IEA, 2007 p.84).
India is currently the second-largest ammonia producer. Ammonia production is responsible for more than 50 percent of the Indian chemical and petrochemical industry's energy use. About 10 percent of ammonia is produced with oil-based processes (see Table 3). In 2010, the average energy use for Indian ammonia production was estimated at 37.7 GJ/tonne of ammonia, while the energy use for the best available technology using natural gas was 28 GJ/tonne of ammonia. The use of oil as feedstock is responsible for half of the gap in these energy intensities (IEA, 2011 p.43). In India, gas-based ammonia-producing plants consume on average 36.5 t NH3, while naphtha-based plants consume 39 t NH3 and fuel oil-based plants 48-87 t NH3 (IEA, 2007 p.85). Further information on the historical developments and future projections regarding energy intensity and CO2 emissions of Indian ammonia plants can be found here.
A shift to natural gas along with the implementation of the best available technology would result in around 25 percent reduction in energy use. In recent years, the increase in oil prices resulted in the rapid decline of oil shares in favor of natural gas. A switch from oil-based to natural-gas based ammonia production in India may also be favored in the future with the recent discoveries of offshore natural gas reserves (IEA, 2011 p.43).
General Industry Characteristics
Top Ammonia Producing Countries in 2011
2012 [1]
Name | Thousand metric tons |
China | 50779 |
India | 14355 |
Russia | 12774 |
United States | 11375 |
Trinidad and Tobago | 6691 |
Indonesia | 6083 |
Ukraine | 5231 |
Canada | 4800 |
TOTAL | 112088 |
2012 [1]
Footnotes
[1] United States Geological Survey:http://minerals.er.usgs.gov/minerals/
Information on some of the international and national organizations who work with improving productivity and resource efficiency in ammonia industry is provided in this section.
Ammonia Organizations Global
Ammonia Organizations Middle East
Ammonia Organizations South Africa
Ammonia Organizations Canada
Ammonia Organizations China
Ammonia Organizations Europe
Ammonia Organizations India
Ammonia Organizations Japan
Ammonia Organizations United States
Programs Description:
Information on international and national programs with relevance to energy efficiency and CO2 emissions in ammonia industry will be provided in this section.
- organizational practices and policies;
- team development;
- planning and evaluation;
- tracking and measurement;
- communication and employee engagement and;
- evaluation and corrective measures (US EPA, 2010).
While an EnMS can help organizations achieve greater savings through a focus on continuous improvement in energy efficiency, it does not guarantee energy savings or carbon dioxide reductions. To achieve cost savings, an EnMS must be combined with effective plant energy benchmarking and appropriate plant improvements.
This page will soon be updated with examples of EnMS implementation in the ammonia industry.
International Energy Agency (IEA), 2007. Tracking Industrial Energy Efficiency and CO2 Emissions.
International Fertilizers Association (IFA), 2009. Energy Efficiency and CO2 Emissions in Ammonia Production, 2008-2009 Summary Report.
International Fertilizers Association (IFA) (2009). Fertilizers, Climate Change and Enhancing Agricultural Productivity Sustainably. Paris, France.
International Energy Agency (IEA) (2012). Energy Technology Perspectives 2012, Pathways to a Clean Energy System. Paris, France. p.329.
International Energy Agency (IEA) (2009). Chemical and Petrochemical Sector: Potential of Best Practice Technology and Other Measures for Improving Energy Efficiency. IEA Information Paper on energy efficiency indicators. Paris, France.