The U.S. Environmental Protection Agency’s (EPA) energy guide, Energy Efficiency Improvement and Cost Saving Opportunities for the U.S. Iron and Steel Industry, discusses energy efficiency practices and technologies that can be implemented in iron and steel manufacturing plants. This guide provides current real world examples of iron and steel plants saving energy and reducing cost and carbon dioxide emissions.
Iron and Steel
Iron and steel are key products for the global economy. Since 2000, global steel production has grown by 75%, reaching 1.49 billion tons of steel in 2011.1 The sector is the largest industrial emitter of CO2 (with direct emissions of 2.16 Gt in 2006) and second largest industrial user of energy (consuming 24 EJ in 2006). Although considerable improvements have been made in recent years, the iron and steel sector still has the technical potential to further reduce energy consumption and CO2 emissions by approximately 20%, saving 4.7 EJ of energy and 350 Mt of CO2.2
Steel production involves numerous process steps that can be laid out in various combinations depending on product mix, available raw materials, energy supply and investment capital. Key characteristics of the three main processing routes are as following:
- In Blast Furnace (BF)/Basic Oxygen Furnace (BOF) route, pig iron is produced using primarily iron ore (70-100%) and coke in a blast furnace, and then turned into steel in a basic oxygen furnace. Due to the inclusion of coke making and sintering operations, this route is highly energy intensive.
- Scrap/Electric Arc Furnace (EAF) route is primarily based on scrap for the iron input and has significantly lower energy intensity compared to the BF/BOF route due to the omission of coke making and iron making processes;
- Direct Reduced Iron (DRI)/EAF route, based on iron ore and often scrap for the iron input. Energy intensity of DRI production can be lower than BF route, depending on the size, and fuel and ore characteristics.
In recent years, there is also increasing attention being paid to smelting reduction, which is emerging as a contender to blast furnace process.
Iron and Steel Schematic
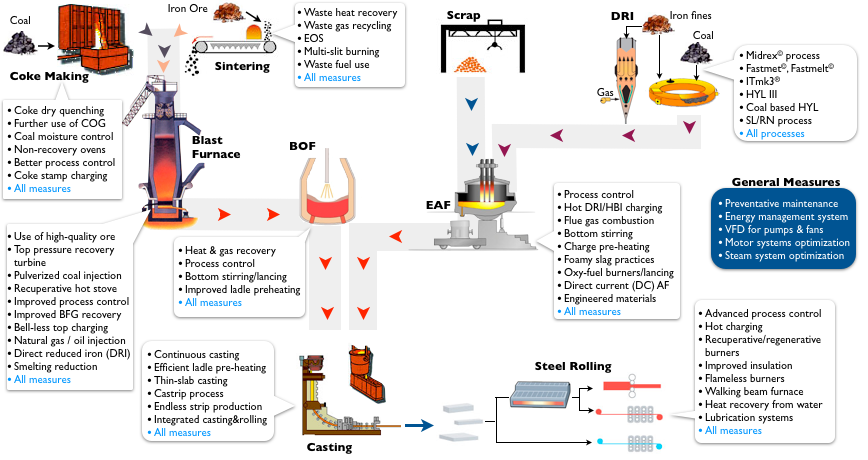
Iron and Steel Processes
Cross-Sectoral Systems
Selected Iron and Steel Technologies & Measures
For a wider list of technologies & measures, please follow the links under processes above.
Products
- Steel
- Iron
Iron and Steel Publications
Energy Efficiency Improvement and Cost Saving Opportunities for the U.S. Iron and Steel Industry
Available and Emerging Technologies for Reducing Greenhouse Gas Emissions from the Iron and Steel Industry
The State–of-the-Art Clean Technologies (SOACT) for Steelmaking Handbook
Date:
Source:
Format:
Type:
The State–of-the-Art Clean Technologies (SOACT) for Steelmaking Handbook is developed as part of the Asia-Pacific Partnership on Clean Development and Climate program and seeks to catalog the best available technologies and practices to save energy and reduce environmental impacts in the steel industry. Its purpose is to share information about commercialized or emerging technologies and practices that are currently available to increase energy efficiency and environmental performance.
Prospective Scenarios on Energy Efficiency and CO2 Emissions in the EU Iron & Steel Industry
Date:
Format:
Type:
The study analyzes the role of technology innovation and its diffusion in the environmental and energy efficiency performance of the Iron and Steel sector from the point of view of the cost-effectiveness of the retrofits of the main process at the plant level and, in particular, for the EU-27 Iron & Steel industry in the medium-to-long term. The report includes a wealth of information on technology options applicable to the iron and steel industry, along with their energy and CO2 performance and cost implications.
Assessment Of Cumulative Cost Impact For The Steel Industry
Date:
Source:
Format:
Type:
This study contains an assessment of the cumulative costs of EU legislation on the European steel industry, as well as an evaluation of how these costs affect the competitiveness of this industry from an international standpoint. Cumulative costs are compared to production costs and current margins of the European steel industry, as well as to the production costs of international steel competitors. The study is commissioned by The European Commission's Directorate-General for Enterprise and Industry and prepared by the Center for European Policy Studies.
Iron and Steel Reference Documents
Best Available Technique (BAT) Reference Document for Iron and Steel Production
Date:
Source:
Format:
Type:
Published by the Joint Research Center of Institute for Prospective Technological Studies (IPTS), that is part of European Commision, this reference document provides detailed information on the Best Available Technologies (BAT) applicable to the iron and steel manufacturing.
Iron and Steel Case Studies
OneSteel – Newcastle Rod Mill
Format:
Type:
This case study examines how OneSteel is embedding energy efficiency into its core business processes. It describes OneSteel's approach to energy efficiency through developing new systems and tools for the Sydney Steel Mills group, which are now being rolled out across OneSteel. As a result, OneSteel is expected to achieve annual energy savings of over 6% of total energy use through adopted savings opportunities identified by its assessments for the Energy Efficiency Opportunities program.
Introduction and Implementation of an Energy Management System and Energy Systems Optimization - Arcelormittal Saldanha Works
Format:
Type:
This case study provides a detailed accounts of introducing and implementing an Energy Management System and Energy System Optimization in Arcelormittal's Saldanha works located in South Africa.
Iron and Steel Presentations
Energy Management Systems in Iron and the Steel Industry
Ladislav Horvath of the World Steel Association presented on EnMS in the iron and steel industry at the China EnMS workshop organized by the Institute of Industrial Productivity. The presentation gives a thorough overview of main energy issues in iron and steel plants, and how these can be effectively addressed by energy management systems.
Due to the high diversity of production processes in the sector, benchmarks based on per ton of product are of limited use. At minimum, there is a need to treat dominating BF/BOF, scrap/EAF, and DRI/EAF routes separately. Even then, there are significant variations in the energy efficiency levels of primary steel production between countries and between plants, due to differences in scale, extent of waste heat recovery, quality of iron ore and fuels, operatinal know-how, automation, and quality control.
The scrap based steel production does not require the ore preparation, coke making and iron making stages necessary for producing iron from the ore in BF/BOF route and is therefore significantly less energy intensive – requiring between 4 to 6 GJ/t as compared to 13 to 14 GJ/t in BF/BOF route. Scrap based production, on the other hand, is limited by the availability of scrap metal.
Iron and Steel Benchmarks
The following table provides best practice energy consumption data for different commonly used process routes for iron and steel production. It should be noted that totals for different process routes highly depend on feedstock and material flows and can show significant variations between different plants. Therefore, comparing individual plants to the totals listed here may be misleading.
Production step | Process | Blast furnace-basic oxygen furnace | Smelt reduction - basic oxygen furnace | Direct reduced iron - electric arc furnace | Scrap-electric arc furnace | ||||
---|---|---|---|---|---|---|---|---|---|
Final | Primary2 | Final | Primary2 | Final | Primary2 | Final | Primary2 | ||
Material preperation | Sintering | 1.9 | 2.2 | 1.9 | 2.2 | ||||
Pelletizing | 0.6 | 0.8 | 0.6 | 0.8 | |||||
Coking | 0.8 | 1.1 | |||||||
Iron making | Blast furnace | 12.2 | 12.4 | ||||||
Smelt reduction | 17.3 | 17.9 | |||||||
Direct reduced iron | 11.7 | 9.2 | |||||||
Steelmaking | Basic oxygen furnace | -0.4 | -0.3 | -0.4 | -0.3 | ||||
Electric arc furnace | 2.5 | 5.9 | 2.4 | 5.5 | |||||
Refining | 0.1 | 0.4 | 0.1 | 0.4 | |||||
Casting & rolling | Continuous casting | 0.1 | 0.1 | 0.1 | 0.1 | 0.1 | 0.1 | 0.1 | 0.1 |
Hot rolling3 | 1.8 | 2.4 | 1.8 | 2.4 | 1.8 | 2.4 | 1.8 | 2.4 | |
Sub-total | 16.5 | 18.2 | 19.5 | 21.2 | 18.6 | 20.6 | 4.3 | 8.0 | |
Cold rolling & finishing | Cold rolling | 0.4 | 0.9 | 0.4 | 0.9 | ||||
Finishing | 1.1 | 1.4 | 1.1 | 1.4 | |||||
Total | 18.0 | 20.6 | 21.0 | 23.6 | 18.6 | 20.6 | 4.3 | 8.0 | |
Alternative: |
0.2 | 0.5 | 0.2 | 0.5 | 0.2 | 0.5 | 0.2 | 0.5 | |
Alternative total: | 14.8 | 16.3 | 17.8 | 19.2 | 16.9 | 18.6 | 2.6 | 6.0 |
Footnotes
Benchmark Footnotes:
Worrell, E., Price, L., Neelis, M., Galitsky, C., Nan, Z. (2008). World Best Practice Energy Intensity Values for Selected Industrial Sectors. Lawrence Berkeley National Laboratory.
For primary energy consumption, losses in converting fuels to electricity and in transmission are taken into consideration. These are assumed to be 67%.
Values are based on energy use for production of hot rolled bars.
According to World Steel Association data, global steel production has increased by about 75% since 2000 and reached 1.49 billon tons of crude steel in 2011. In the same period, iron produced in blast furnaces and using direct reduction processes increased by 88% and 45%, reaching 1 080 and 64 million tons, respectively. Although there has been significant increase in scrap use in steel-making, in 2011 a higher share of steel was produced from iron derived from ore, than in 2000 (BF+DRI/steel ratios in 2000 and 2011 are 0.73 and 0.76, respectively).
The six largest producers (China, Japan, the United States, India, Russia and South Korea) accounted for 73% of total world steel production in 2011.
The iron and steel sector is the second-largest industrial user of energy, consuming 24 EJ in 2006, and the largest industrial source of CO2 emissions.
There are many proven technologies and practices that can significantly reduce the energy demand and CO2 generation in this sector. Some of the major technologies and their estimated potential for different regions are presented in the figure below.
General Industry Characteristics
Top Six Steel Producers and their Share in Global Production
2011 [1]
Name | Mt |
China | 683.3 |
Japan | 107.6 |
United States | 86.2 |
India | 72.2 |
Russia | 68.7 |
South Korea | 68.5 |
Rest of the World | 403.5 |
TOTAL | 1490 |
2011 [1]
Footnotes
[1] World Steel Association:http://www.worldsteel.org/statistics/top-producers.html
There are numerous organizations working at global, regional, national levels to improve the resource productivity and reduce the environmental impact of iron and steel manufactuing. Some of the major ones are listed below:
Iron and Steel Organizations Global
Iron and Steel Organizations Asia-Pacific
Iron and Steel Organizations Australia
Iron and Steel Organizations Brazil
Iron and Steel Organizations China
Iron and Steel Organizations Europe
Iron and Steel Organizations European Union
Iron and Steel Organizations India
Iron and Steel Organizations United States
Iron and Steel Organizations Japan
Iron and Steel Programs Australia
Iron and Steel Programs China
Iron and Steel Programs European Union
Iron and Steel Programs India
Iron and Steel Programs Japan
Iron and Steel Programs United States
There are a number of guidelines aimed at helping companies to establish an effective EnMS - including those from United States Environmental Protection Agency (US EPA) and the recent ISO 50000 series of the International Standards Organization.
Although they may differ in their details, these guidelines promote continuous improvement of energy efficiency through:
- Organizational practices and policies;
- Team development;
- Planning and evaluation;
- Tracking and measurement;
- Communication and employee engagement; and;
- Evaluation and corrective measures (US EPA, 2010)
The major elements of a strategic energy management system is depicted in the Figure.
A sound energy management program is required to create a foundation for positive change and to provide guidance for managing energy throughout an organization. Continuous improvements to energy efficiency therefore typically only occur when a strong organizational commitment exists. Energy management programs help to ensure that energy efficiency improvements do not just happen on a one-time basis, but rather are continuously identified and implemented in a process of continuous improvement.
While EMSs can help organizations achieve greater savings through a focus on continuous improvement, they do not guarantee energy savings or carbon dioxide reductions alone. Combined with effective plant energy benchmarking and appropriate plant improvements, EMSs can help achieve greater savings.
Iron and Steel Case Studies
OneSteel – Newcastle Rod Mill
Format:
Type:
This case study examines how OneSteel is embedding energy efficiency into its core business processes. It describes OneSteel's approach to energy efficiency through developing new systems and tools for the Sydney Steel Mills group, which are now being rolled out across OneSteel. As a result, OneSteel is expected to achieve annual energy savings of over 6% of total energy use through adopted savings opportunities identified by its assessments for the Energy Efficiency Opportunities program.
Introduction and Implementation of an Energy Management System and Energy Systems Optimization - Arcelormittal Saldanha Works
Format:
Type:
This case study provides a detailed accounts of introducing and implementing an Energy Management System and Energy System Optimization in Arcelormittal's Saldanha works located in South Africa.
Iron and Steel Presentations
Energy Management Systems in Iron and the Steel Industry
Ladislav Horvath of the World Steel Association presented on EnMS in the iron and steel industry at the China EnMS workshop organized by the Institute of Industrial Productivity. The presentation gives a thorough overview of main energy issues in iron and steel plants, and how these can be effectively addressed by energy management systems.
World Steel Association, 2012.
International Energy Agency (2009) Energy Technology Transitions for Industry.