The U.S. Environmental Protection Agency’s (EPA) energy guide, Energy Efficiency Improvement and Cost Saving Opportunities for the U.S. Iron and Steel Industry, discusses energy efficiency practices and technologies that can be implemented in iron and steel manufacturing plants. This guide provides current real world examples of iron and steel plants saving energy and reducing cost and carbon dioxide emissions.
Heat Recuperation from Hot Blast Stoves
Hot blast stoves typically require about 3 GJ/t-HM and account for about one third of the enrgy needed to make iron and around 10–20% of the total energy demand in integrated steel works. The efficiency of the hot stoves can be improved by recovering the heat from the flue gases of the stoves (having typical temperatures of around 250 oC (Worrell, 2010. et al., p. 87);and using this energy to pre-heat the combustion fuel and/or the air entering the stoves. Besides stove flue gases, other heat sources, such as that arising from sinter cooling, can be used for this purpose. While also reducing the need and costs for natural, or any other enriched, gas, pre-heating with waste heat increases the oeverall stove efficiency by up to 8% (IEA, 2007. p.126). Recuperated heat from BF stoves can also be used to preheat the BF air itself, or to heat the gas and/or combustion air used for boilers and other heating systems located in close proximity. For each application, the system and control requirements will be different and the final system should be selected based on fuel reduction potential and cost effectiveness. In most cases one of these options is justifiable.
This option is regarded to have medium application potential in China and India, and low potential for the United States.
Development Status | Products |
---|---|
Commercial
|
Heat Recuperation from Hot Blast StovesCosts & Benefits
Parent Process: Blast Furnace System | |
---|---|
Energy Savings Potential |
This technology can reduce the energy demand by 0.24 GJ/t-HM. Its global application has 0.2 EJ/y energy reduction potential (EIA, 2007. p.126). Energy savings can be as much as 0.3 GJ/t-pig iron (Worrell, 2010. et al., p. 87) Various systems allowing fuel savings between 80 to 85 MJ/t-HM have been installed. (US EPA, 2010. p. 20)
|
CO2 Emission Reduction Potential |
With global application of this technology, CO2 emissions could potentially be reduced by 20 Mt annually (EIA, 2007. p.126) |
Costs |
|
Heat Recuperation from Hot Blast StovesSchematic
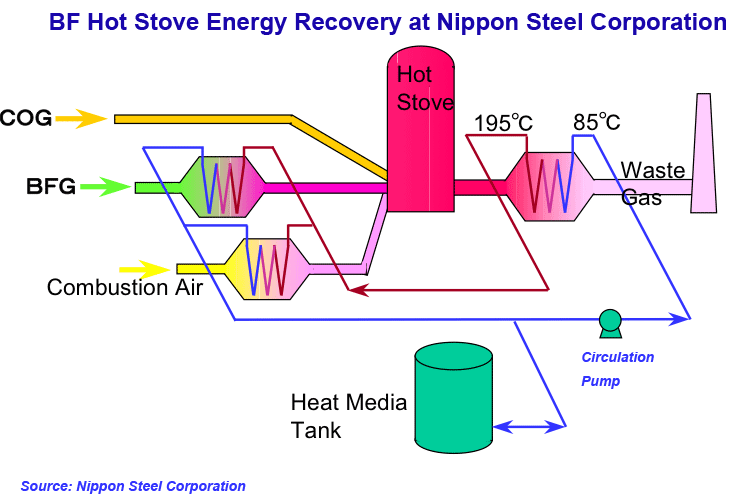
Heat Recuperation from Hot Blast Stoves Publications
Energy Efficiency Improvement and Cost Saving Opportunities for the U.S. Iron and Steel Industry
Page Number:
Global Warming Countermeasures: Japanese Technologies for Energy Savings / GHG Emissions Reduction
Date:
Source:
Format:
Type:
This revised 2008 version of the publication from New Energy and Industrial Technology Development of Japan includes information on innovative Japanese technologies for energy efficiency and for the reduction of CO2 emissions.