The U.S. Environmental Protection Agency’s (EPA) energy guide, Energy Efficiency Improvement and Cost Saving Opportunities for the U.S. Iron and Steel Industry, discusses energy efficiency practices and technologies that can be implemented in iron and steel manufacturing plants. This guide provides current real world examples of iron and steel plants saving energy and reducing cost and carbon dioxide emissions.
Rolling Mills
In rolling mills, intermediate steel products are given their final shape and dimension in a series of shaping and finishing operations. Most of the slabs are heated in reheating furnaces and rolled into final shape in hot– or cold–rolling or finishing mills. While some products (e.g. reinforcement bars, steel plates) only require hot-rolling, some others may require both hot– and cold–rolling (steel for cars and white-goods). Mechanical forces for cold rolling will create much more force and energy needs, while hot rolling happens much faster with less forces; however, there are significant energy costs to heat the metal to near eutectic temperatures (US EPA, 2010. p.25). In large integrated steel plants, the hot strip rolling process is the third largest user of energy after iron and steel making (IEA, 2007. p. 135).
In any hot rolling operation the reheating furnace is a critical factor to determine end-product quality, as well as the total costs of the operation. Energy use in a reheating furnace depends on production factors (e.g. stock, steel type), operational factors (e.g. scheduling), and design features. Based on seven sites, average total primary energy requirement of 1.2 GJ/t-cast steel is reported for hot rolling. According to IEA (2007), globally, typical hot rolling energy needs are 2 – 2.4 GJ/t.Upgrading existing furnaces will be another way of harvesting energy savings.
According to IEA (2007) global average energy needs in cold rolling are between 1 – 1.4 GJ/t.
Rolling MillsSchematic
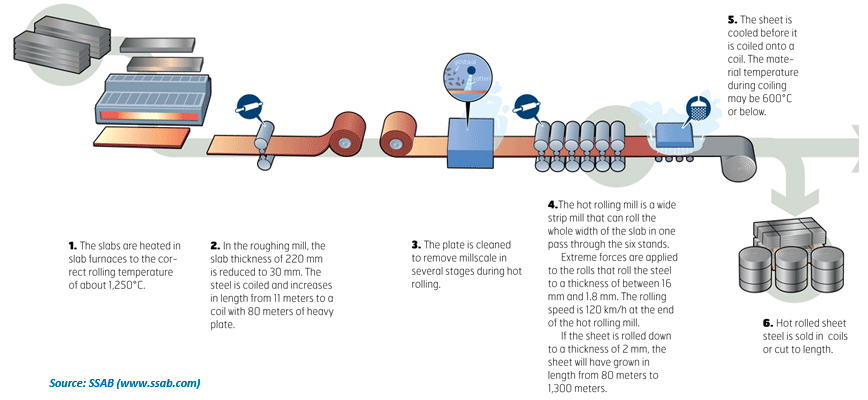
Rolling MillsTechnologies & Measures
Technology or Measure | Energy Savings Potential | CO2 Emission Reduction Potential Based on Literature | Costs | Development Status |
---|---|---|---|---|
Process Control in Hot Strip Mill |
Estimated energy savings based on reducing rejects from 1.5% to 0.2% was 9% of fuel use, or approximately 0.3 GJ/t-product (US EPA, 2010. p.27). |
Emissions are reduced by 15.1kg CO2/t-rolled steel. |
The investment costs for one plant in Belgium was $3.6 million for a hot strip mill with a capacity of 2.8 million tons, $1.29/t-product. The payback time is estimated as 1.2 years (US EPA, 2010. p. 27). |
Commercial |
Proper Reheating Temperature |
A reduction of the heating temperature 100°C in the reheating furnace decreases unit fuel consumption by 9% to 10%. However under certain conditions total energy consumption may not decrease with a decrease in heating temperature. |
Commercial | ||
Throughput Optimisation in Rolling Mills |
This technology ensures better utilization of rolling mill capacity and optimises throughput. Energy Saving occurs through improved product flow. |
Coupling of work processes in case of interruptions, thereby less wear occurs. |
Commercial | |
Oxgen Level Control and VSDs on Combustion Fans |
A conservative approach estimates energy savings to be around 10%, or 0.33 GJ/t-rolled steel. |
Emissions are reduced by 16.6 kg CO2/t-rolled steel. |
Retrofit capital costs are estimated at $0.79/t-rolled steel. |
Commercial |
Pressure Control for Furnace |
LPG consumption was reduced by 83.3 tons/y in a drying furnace. Electric power savings were 24,734kWh/y. |
Lower emissions due to energy savings by the technology. |
Cost savings are ¥413,000/y. |
Commercial |
Avoiding Furnace Overloading |
Energy consumption per unit production will decrease. |
CO2 reductions per unit production will decrease. |
Not available. |
Commercial |
Energy Efficiency Drives for Rolling Mills | High efficiency motors can save approximately 1-2% of the electricity consumption. Assuming an electricity demand of 220 kWh/t-hot rolled steel, the electricity savings are estimated to be 4 kWh/t-product (Worrell et al., 2010. p.100). |
Emission reductions are estimated at 1.6 kg CO2/t-product. |
The additional cost of the high efficiency drives was estimated to be approximately $0.30/t-hot rolled steel. The payback time is estimated as 3.2 years (US EPA, 2010. p. 25). | Commercial |
Regenerative Burners for Reheating Furnaces |
NEDO reports that using regenerative burners on a 110 t/h capacity billet reheating furnace (operating at 1050 oC) can reduce the energy consumption by 0.18 to 0.21 GJ/t-steel, as compared a conventional furnace. Annual energy savings are reported to be 9.3 to 11.6 GWh ((NEDO, 2008. p. 88) |
Up to 50% NOx reduction is possible with high temperature combustion. CO2 emissions will also be reduced according to the reduced fuel consumption. |
Retrofiting costs for three pairs of regenerative burners for a 110 t/h furnace were ¥9 million for equipment and ¥1 million for construction. |
Commercial |
Flameless Burners - Dilute Oxygen Combustion |
|
|
Commercial | |
Walking Beam Furnace |
Compared to three pusher type of furnaces, installation of a walking beam furnace together with a state-of-the-art control system reduced energy and fuel consumption by 25% and 37.5%, respectively. |
Lower operational costs compared to alternative transmission systems. |
Commercial | |
Recuperative Burners |
Recuperative burners in the reheating furnace can reduce energy consumption by as much as 30 percent. Although actual savings will be highly facility-specific, one estimate placed energy savings at approximately 0.7 GJ/t-product.
|
|
Retrofit Capital Cost is $3.9/tonne rolled steel. |
Commercial |
Thermochemical Recuperation for High Temperature Furnaces |
This technology can reduce the fuel consumption in the furnace by 25% or more. |
CO2 and NOx emissions will be reduced. |
Demonstration | |
Installing Lubrication Systems |
Installation of a lubrication system resulted savings of 4 kWh/t-product (Worrell et al., 2010. p. 100). |
Savings are estimated at $0.31/t-product. |
Commercial | |
Improved Insulation of Reheating Furnace |
The potential energy savings for insulating a continuous furnace were estimated to range from 2 to 5% or around 0.16 GJ/t-rolled Steel. |
Emissions reductions are estimated to be around 8.0 kg CO2/t-rolled steel. |
Retrofit Capital cost of $15.6/tonne solled steel is estimated. |
Commercial |
Hot Charging |
Energy savings of 0.06 GJ/t-rolled steel are estimated (US EPA, 2010. p.27).
|
Emissions reduction potential is estimated to be 30.2 Kg CO2/t-rolled steel. |
Retrofit capital costs and savings are estimated as $23.5/t-rolled steel and $1.15/t-hot charged steel with payback times of 5.9 years (US EPA, 2010. p.27).
|
Commercial |
Cold Rolling - Reducing Losses on Annealing Line |
Implementing loss reduction measures for a continuous annealing line, energy use can be reduced by up to 40-60% compared to furnaces without heat recovery (Worrell et al., 2010. p. 105). Energy savings can amount to 0.3 GJ/t-product for fuel and 0.011 GJ/t-product for electricity (US EPA, 2010. p. 29). |
Emission reductions are estimated to be 17.5 kg CO2/t-product. |
Investment costs in a plant in Netherlands were estimated to be $4.2/t-product. The payback time is estimated as 4 years (US EPA, 2010. p. 29). |
Commercial |
Cold Rolling - Automated Monitoring and Targeting System. |
A system installed at the UK based strip mill reduced energy demand of the cold rolling mill by approximately 15-20% (Worrell et al., 2010. p. 104) or approximately by 0.22 GJ/t-product (US EPA, 2010. p. 30). |
|
Installation costs were estimated to be $1.72/t-product, or $1.0/t-crude steel. The payback time is estimated as 0.8 years. |
Commercial |
Cold Rolling - Reduced Steam Use in the Acid Pickling Line |
Steam use can be reduced by around 17% or by approximately 0.19 GJ/t-product (US EPA, 2010. p. 30). |
Emission reductions are estimated to be 9.9 kg CO2/t-product (US EPA, 2010. p. 10). . |
Estimated capital costs were $4.4/t-product. The payback time is estimated as 7 years (US EPA, 2010. p. 30). |
Commercial |
Cold Rolling - Continuous Annealing Furnace |
In a Japanese plant installation of this system reduced fuel consumption by 33%. > |
|
Commercial | |
Heat Recovery to the Product |
Annual cost savings of 32% compared to no-heat recovery. |
Commercial | ||
Heat Recovery from Cooling Water |
Energy savings of 0.0 GJ/t-rolled steel is estimated by the implementation of the technology, with an increase of 0.17 kWh/t in electricity consumption (Worrell et al., 2010. p. 104). |
Emission reductions are estimated at 1.9 kg CO2/t-rolled steel (US EPA, 2010. p.10). |
Retrofit Capital Cost is $1.3/t-rolled steel. Operation and maintenance costs can increase by $0.11/t-product (US EPA, 2010. p. 29). |
Commercial |
Thin Slab Casting - Near Net Shape Casting |
TSC is estimated to reduce energy consumption by 4.9 GJ/t-crude steel. |
Thins slab casting is estimated to reduce CO2 emissions by 779 kg per ton of product. |
Investment costs for a large-scale plant were estimated to range from $234.9/t-product with a resultant cost savings of approximately $31/t-crude steel. |
Commercial |
Endless Strip Production (ESP) |
Specific energy consumption decreases by 40 – 60% as compared to a traditional rolling mill. |
Environmental emissions will drastically decrease due to reduced energy consumption by avoiding reheat furnaces. |
Commercial | |
Strip Casting – Castrip® Process |
Compared to thick slab casting (hot rolling, pickling and cold rolling), the Castrip® process saves approximately another 2 GJ/t. |
Correleating from the energy savings reported in APP (APP, 2010. p.94), the process is estimated to redcue CO2 emissions by 80-90% comparing to conventional casting. |
Commercial | |
Integrated Casting and Rolling |
Energy savings can range from 35% to close to 100%. |
CO2 emissions are reduced due to reduced fuel consumption. |
Commercial | |
Thin Slab Casting |
Energy savings are in range of 1 – 2 GJ of Primary Energy/t of product. Saving potential is 0.3-0.4 EJ/yr if this technology is applied to quarter of world production. |
Estimated CO2 emissions savings are 20 - 40 Mt/yr. |
Retrofit capital cost is $234.9/tonne hot rolled steel. |
Commercial |
Strip Casting |
The savings over traditional thick slab continuous casting include 0.32-0.55 GJ/t for electricity and 1.2-1.5 GJ/t for fuel (US EPA, 2010. p.25). |
Commercial | ||
Novel Post Combustion Method |
Savings of up to 30% in fuel gas have been achieved relative to recuperative combustion air preheating systems. |
Reduction of pollutants because flue gas is utilized. |
Further cost reductions are possible due to the use of inexpensive low calorific-value gases such as process and biogas. |
Demonstration |
Model Based Closed-Loop Oxygen Control |
By reducing the oxygen content by 1.5 % in a heating furnace with a throughput of 450 t/h, energy consumption was reduced by 2.4 %. |
For a 450 t/h capacity furnace, cost savings due to reduced energy consumption were €350 thousand/y. |
Demonstration | |
Preventing Scale Formation in Rolling |
Energy consumption and material loss will be reduced. |
Reduced energy and material costs, and minimisation of subsequent corrective measures will reduce the costs. |
Research | |
Extended Universal Fuel Gas Measuring Device | Research | |||
Innovative Reheat Furnace Management |
This technology improves the performance of the furnace and its energy efficiency. It is possible to reduce the oxygen concentration to approximately 7 % by volume. |
This technology lowers CO2 emissions. |
The energy costs will be lowered. |
Demonstration |
High Temperature Membrane Module for Oxygen Enrichment of Combustion Air |
Savings of natural gas is estimated. Process gas can be reused. |
This technology will decrease anthropogenic CO2 emissions. |
If the O2 can be provided cost-efficiently,this will reduce operating costs of the technology. |
Research |
Development of Oxygen-rich Furnace System for reduced CO2 and NOx emissions |
By applying this technology, fuel firing rate was decreased from 325-365 KW to 200-220 KW. |
Potential savings are 40 – 45% in fuel usage. A corresponding reduction in CO2 emissions is obvious. |
Fuel savings are offset to some extent by the cost of the Oxygen. However O2 production technologies are becoming more economical. |
Demonstration |
Oscillating Combustion |
Efficiency or productivity increases by 5% or more. It improves heat transfer by up to 13%. |
The technology reduces NOx emissions by up to 75%. |
Demonstration |
Rolling Mills Publications
Energy Efficiency Improvement and Cost Saving Opportunities for the U.S. Iron and Steel Industry
Page Number:
Available and Emerging Technologies for Reducing Greenhouse Gas Emissions from the Iron and Steel Industry
Page Number:
Global Warming Countermeasures: Japanese Technologies for Energy Savings / GHG Emissions Reduction
Date:
Source:
Format:
Type:
This revised 2008 version of the publication from New Energy and Industrial Technology Development of Japan includes information on innovative Japanese technologies for energy efficiency and for the reduction of CO2 emissions.