The U.S. Environmental Protection Agency’s (EPA) energy guide, Energy Efficiency Improvement and Cost Saving Opportunities for the U.S. Iron and Steel Industry, discusses energy efficiency practices and technologies that can be implemented in iron and steel manufacturing plants. This guide provides current real world examples of iron and steel plants saving energy and reducing cost and carbon dioxide emissions.
Basic Oxygen Furnace
Basic Oygen Furncace (BOF) is a pear shaped vessel where the pig iron from blast furnace, and ferrous scrap, is refined into steel by injecting a jet high-purity oxygen through the hot metal. More specifically, in a BOF:
- the carbon content of pig iron, which is typically 4-5%, is reduced to varying levels below 1% depending on the product specifications;
- unwanted impurities are removed;
- concentration of desired is brought to product specifications.
Approximately 50 Nm3 of oxygen, which is produced in another plant, is required for every ton of liquid steel. As the reactions taking place in the BOF are highly exothermic, the temperatures in the furnace usually reach 1600-1650 oC. Scrap, or scprap substitutes, that meet purity requirements are often added to control excessive temperature rises. However, the pig iron input stays at the levels of 65 to 90% for every ton of steel produced. Impurities are dissolved by the added limestone and fomed into a slag. During the BOF processes a gas with high CO content is formed. If no gas recovery is exercised, CO is converted to CO2 by combustion at the mouth of the furnaces with open hood, and through flaring after gas cleaning in furnaces with a closed hood. BOF shops are often followed by secondary metallurgy processes - in laddle or in vacuum - to give the product its final characteristics. BOF operations can be a net producer of energy if the sensible and chemical energy leaving the furnace is recovered and utiliized (Worrell, et al., 2010. p. 13-14)
Basic Oxygen FurnaceSchematic
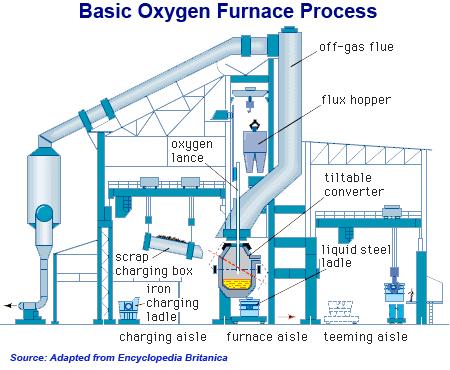
Basic Oxygen FurnaceTechnologies & Measures
Technology or Measure | Energy Savings Potential | CO2 Emission Reduction Potential Based on Literature | Costs | Development Status |
---|---|---|---|---|
BOF Heat and Gas Recovery |
With the combustion method 0.125 GJ/t-steel can be recovered (NEDO, 2008) With the non-combustion method savings can be in the range of 0.54 and 0.92 GJ/t-steel, depending on how the steam is used. Energy reduction potential with the worldwide applicaiton of the BOG gas recovery is estimated to be 250 PJ. (IEA, 2007. p. 127)
|
CO2 reductions can be reduced approximately by 50 kg/t-steel with this measure (US EPA, 2010. p. 22) Worlfwide recovery of BOF gas can reduce CO2 reductions by 25 Mt/y. (IEA, 2007. p. 127).
|
For a 110 t/charge capacity plant in Japan, the equipment costs for non-combustion technology was reported to be ¥600 to 1100 million. For this plant the payback time is estimated to be 8.3 to 15 years. (NEDO, 2008)
The capital cost of the recovery system is estimated at roughly $20/t-steel (or approximately $66 million for an average BOF shop with a production rate of 2.7 million t/. The payback period is estimated as 12 years (US EPA, 2010. p. 22) Retrofit capital costs are $34.4/tonne steel. According to an experts opinion, the installation costs vary in a wide range depending on the scope of supply and the country of installation. Basically the Return of Investment is between 2,5 and 4 years. Payback is a strong function of the natural gas prize.
|
Commercial |
BOF Bottom Stirring |
Flux quantities are reduced by more than 10%. Less Iron is Lost to slag. Oxygen consumption is reduced. |
Costs can be reduced because Vacuum Treatment process is not required. Vessel life is also prolonged. |
Commercial | |
Aluminum Bronze Alloy to Improve Hood, Roof and Sidewall Life |
More than 5.6 TJ/y energy saving is claimed with a BOF skirt installation, and additional 4.2 TJ/y potential is indicated with application in other system components. |
CO2 emission reductions of 550 metric tons/year are reported from the pilot application. |
Maintenanace costs are 5% comparing with former maintenance. |
Demonstration |
Improved Process Monitoring and Control |
Total energy savings due to oxygen management system is estimated to be 1.5% of the electricity used for Oxygen production. |
These technologies help reduce direct and indirect emissions. |
These process control measures improve productivity and prolong equipment life-time, both providing economic benefits. |
Commercial |
Improved Ladle Preheating |
|
Reduction in fuel consumption results in lower emissions. |
|
Commercial |
Variable Frequency Drives on Ventilation Fans |
This technology reduces the power demand by approximately 20%, or 1.0 kWh/t-steel. |
Emissions reduction of 0.51 Kg CO2/tonne liquid steel is estimated. |
Retrofit capital cost is approximately $1.7 million, or $0.31/t-liquid steel. |
Commercial |
ProVision Lance-Based Camera System for Vacuum Degasser |
It reduces energy use due to reduced processing time. |
Potential emission reductions per installation per year are 550 tons CO2 . NOx emissions reduces by 2.5 tons NO2. |
Assuming a 330 day production Year and $40 per tonne profit yields an annual profit increase of $0.870 Million. |
Commercial |
Laser Contouring System |
It reduces energy usage via rapid real-time measurement and no loss of process time occurs. |
Ladle lifetime extension does create the opportunity for reduced consumption of raw material and refractory landfill usage. |
At $40 per ton profit, this equates to a net profit Increase of $3,520 per day or $1.1 M (Profit) over a 330 day work year. |
Commercial |
Automated Steel Cleanliness Analysis Tool |
Energy savings are estimated to be at least 3.2 billion MJ per Year or about 0.25% of the steel industry energy consumption |
Successful industry wide implementation will reduce waste in processing. It saves the steel Industry at least $40 million annually. |
Research | |
MultiGas Analyzer |
This technology potentially lowers CEM operational energy use by 70%. |
It reduces environmental emissions. |
Lower operation costs, reduced maintenance and performance verification time result in labor savings of up to 80%. |
Commercial |
In-Situ Real-Time Measurement of Melt Constituents |
Commercial cost ranges from $750000 to $2 million. A US-DOE project aims at producing the system costing less than $100,000. |
Demonstration | ||
Improving System Life of BOF and EAF Hoods,Roofs and Side Vents |
Technology saves more than 5.3 billion Btu per year in a BOF skirt installation, with an additional 4 billion Btu annual savings from installations in other system components. |
It reduces CO2 emissions by 550 metric tons/year. |
Maintenanace costs are 5% comparing with former maintenance. |
Commercial |
Steel Slag Usage in Cement |
The material requires little or no additional fuel to convert it into cement clinker. |
The credits are roughly 0.6 t CO2/t clinker substitute. The total savings potential is approx 50 Mt CO2 (IEA, 2007). |
Technology can easily be Integrated into virtually any existing cement plant at low capital cost. |
Commercial |
Recycling of BOF steelmaking slag |
Iron recovered from BOF slag saves 10.5 GJ/t-steel. |
Demonstration |