Direct Reduced Iron
Direct Reduced Iron (DRI), also known as Sponge Iron, offers an alternative steel production route to BF-BOF and Scrap-EAF routes. In DRI, iron ore is reduced in its solid state – unlike BF process where a liquid metal is formed during reduction. DRI can then be transformed to steel in electric arc furnaces. DRI production is common in Middle East, South America, India and Mexico. DRI offers an attractive option due to its small scale low capital investment requirements and its suitability to local raw material situations. Consequently production has been expanding rapidly over the past three decades. However, the small scale of DRI operations also act as a barrier for energy efficiency investments.
Natural gas and coal are the two primary fuels used in DRI production. Whereas more than 90% of the global DRI plants use (lower grade) natural gas, production in India is primarily coal based. The energy consumption in natural gas based DRI production is well known and established to be 10.4 GJ/t-DRI. Natural gas based DRI production also leads to lower CO2 emissions, with emissions ranging from 0.77 to 0.92 ton of CO2 per fon of steel, depending on the type of electricity used. The most common technologies used for DRI production are MIDREX and HYL III, both using natural gas (IEA, 2007. p.132).
DRI processes can be divided up by the type of reactor employed, namely:
- shaft furnaces (Midrex®, HyL)
- rotary kilns (SL/RN process)
- rotary hearth furnaces (Fastmet®/Fastmelt®, and ITmk3®)
- fluidised bed reactors (Circored®) (IPPC, 2009)
As there is no melting and no slag phase in DRI production, all gangue elements of the iron ores remain in the DRI and need to be separated via a slag in the EAF. This increases the electrical energy consumption of the EAF compared to steel scrap melting. If hot DRI is immediately transferred to the EAF melt shop, the heat from the direct reduction process lowers the cost of melting the DRI in the EAF, significantly cutting these energy costs and electrode consumption (IEA, 2009. p.68)
In DRI production India deserves special attention, not only because the country is the larges producer of DRI, but also because production is primarily coal based. In india DRI plants can be easily erected with the help of local suppliers, and the investment in a 100 t/d capacity DRI plant can be recovered in 12 to 18 months. There is a large number of DRI producers in India, and their numbers are continuously increasing.
Thermal loads for DRI production are mainly linked to the quality of coal and to a lesser degree to the reducibility of iron ore. High proportion (32% on average) of non combustible constituents (ash and moisture) of the coal commonly used in the Indian DRI plants result in higher specific energy consumption. Typical coal use in Indian DRI plants is in the range of 1.2 to 1.5 t-coal/t-DRI. The coal use in advanced plants is between 1.05 – 1.2 t-coal/t-DRI, which equals 20 – 25 GJ/t-DRI. This is significantly larger than the 15 - 19 GJ/t-DRI value obtained by using coal with 16% non-combustable fraction in South Africa. The counter-current rotary kilns used for DRI production in India only allow about 60% of the heat to be used for reduction, revalorization of the remaining 40% that is discharged from the kiln offers a significant potential for energy efficiency improvements. (IEA, 2007. p. 132-133)
Direct Reduced IronSchematic
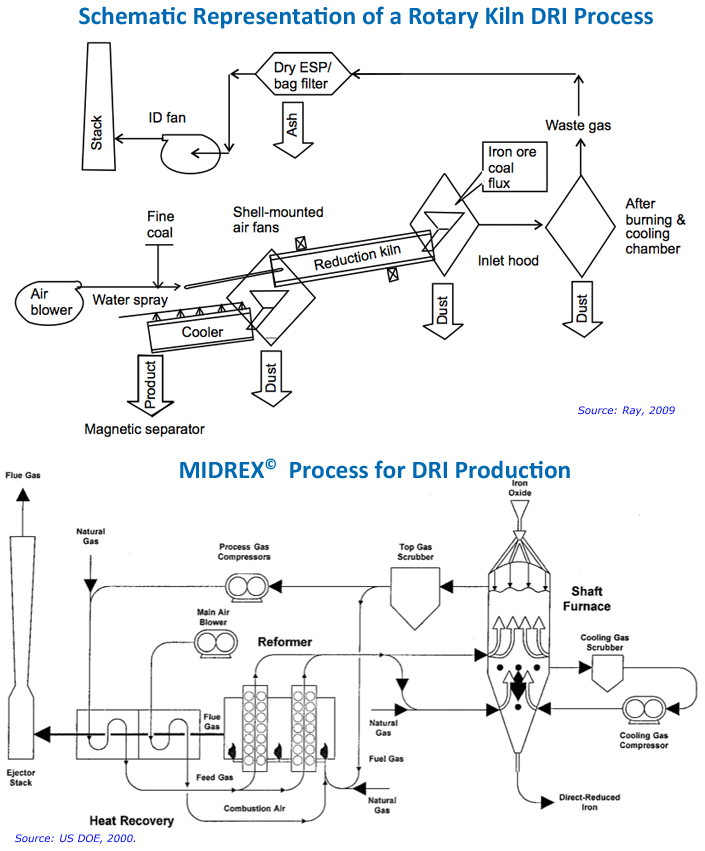
Direct Reduced IronTechnologies & Measures
Technology or Measure | Energy Savings Potential | CO2 Emission Reduction Potential Based on Literature | Costs | Development Status |
---|---|---|---|---|
Midrex© Process | Total primary energy demand of the process is around 10.4 GJ/t. The natural gas consumption of eficiency Midrex plants are aruond 9.62GJ/t-DRI. | Some MIDREX plant/EAF facilities emit only one-third of the CO2 per tonne of steel of a BF/BOF complex (IEA, 2009. p.68) | Commercial | |
HYL III Process | The energy consumption of the process is 10.4 GJ/t-DRI. | IEA reports that CO2 emissions of steel produced from 100% natural gas based DRI is between 0.77 to 0.92 t-CO2/t-steel. | Commercial | |
FASTMET© & FASTMELT© |
Energy consumption of the technology is 12.3 GJ/t-HM (APP, 2010. p.53). |
Fastmet process reduces CO2 emissions by 1,24 t/t-HM (APP, 2010. p. 53). |
Commercial | |
ITmk3® Process |
This technology reduces energy consumption by 3 GJ/t-HM and 10 GJ/t-HM as compared to large- and small-scale blast furnaces. No electrictiy is used (Tanaka 2007. p. 10). |
CO2 reduction of 1 tCO2/t-HM is expected. |
Commercial | |
Midrex with CO2 Removal System |
This process is reported to reduce natural gas consumption. |
According to the information provided by the company, If the removed CO2 is used for enhanced oil recovery, sequestered underground, or sold into a pipeline, stack CO2 emissions per ton of DRI are reduced by 250 kg/t DRI, about 50%. |
Midrex expects that in most cases, the technology will result in a net decrease in operating cost. |
Commercial |
MXCOAL™ - Midrex© with Coal Gasification |
Not available |
Not available |
Low quality and low cost coal is used. |
Demonstration |
Coal-Based HYL Process |
This technology does not require coking coal, coke and natural gas. Production of hot DRI that could be charged to EAF to achieve significant energy savings. |
Environmental benefits are comparable to Blast Furnace route. |
Low quality and low cost coal is used. |
Commercial |
Dust Recylcing in Rotary Hearth Furnace |
Fuel ratio of BF decreases to 0.2kg/t-Pig Iron. JSIM reports the energy saving of 1400 TJ/year achieved by installing 2 units of this system in Japan. |
Lower emissions due to reduced energy consumption. |
This technology results in waste reduction and therefore decreases the disposal costs. |
Commercial |
SL/RN Process |
Energy consumption decreases because no coke oven and sinter plants are required. Total electricity consumption is 999.74 kWh/metric ton liquid steel. |
Total CO emissions are 3.2 t/t-liquid steel. |
Investment and operational costs of the process are reported to be $344.4 and $183.1 per ton of steel, based on a scrap cost of $120/t-scrap (US DOE, 2003. p. 4/4.) |
Commercial |
Waste Heat Recovery for Rotary Kiln Direct Reduction |
The coal consumption is about 800 kg/t DRI. |
Significant CO2 and particulate matter emissions are the limitations of the process. |
Low capital cost is expected since pelletizing or sinter plants are not required. |
Commercial |
Finmet |
Finmet process gas usage is 12.4 GJ/t-DRI which is lower than Blast Furnace. |
Installation costs for a 1.0–1.1 Mt/y plant was reported to be ~ €165 million for equipment and ~€35 million for construction (VATech, 2003) Capital cost investments are estimated to be $263.5/t-steel. Operational costs are estimated at $185/t-steel (with a scrap cost of $120/t-scrap) (DOE, 2003. p.21, 25) |
Commercial | |
Iron Carbide Process |
Energy input to the process is reported to be 12.6 GJ/t-product (IPPC, 2009. p.500). |
Total CO2 emissions from the process are reported to be 2.17 t CO2/t-steel. |
Capital expenses for the process are estimated to be $347.6/t-steel. |
Commercial |
Circored |
Gas usage of the process is reported to be 11.5 GJ/t which is lower than Blast Furnace (IEA, 2007. p. 133). Electricity consumption per ton of liquid steel produced through Circored-HBI-EAF route is reported to be 901 kWh/t-steel (US DOE, 2003. p.4/24). |
Process related and total (including electricity) CO2 emissions of the process are reported to be 1.2 and 2.02 t/t-steel (US DOE, . |
Capital and operational costs for the process is reported to be $232.4/t-steel and $185.3/t-steel (based on scrap cost of $120/t-scrap) (US DOE, 2003. p.4/4) |
Commercial |
Redsmelt |
Less energy usage since no coke oven is required. Electricity consumption is estimated to be around 690.3 kWh/t-steel (US DOE, 2003. p.4/4). |
Total CO2 emissions of the process are estimated to be around 1.992 tCO2/t-steel (US DOE, 2003. p.4/4). |
Capital and operational costs are estimated at $334.7 and $190.7/t-steel, respectively (US DOE, 2003. p.4/4). |
Commercial |
Sustainable Steelmaking using Biomass and Waste Oxides |
Productivity gains as high as 50% could be achieved replacing coal with Wood Charcoal. An Increase of less than 5% in total carbon consumption is achievable. |
If Wood charcoal is used for Iron production net CO2 and sulfur emissions can be significantly reduced. |
Research | |
Suspended Hydrogen Reduction of Iron Oxide Concentrates |
This technology will require ~ 38% less energy than the blast furnace process or 7.4 GJ/ton of hot metal. |
Even when natural gas or coal is used significant reduction in carbon dioxide emissions 39% and 69% of the Blast Furnace value, respectively are estimated. |
Low cost raw materials can be used. |
Research |
ULCORED |
This technology will consume less energy than other natural gas based DRI technologies. |
Reduction in emissions will occur when the technology is Used with CCS. |
Cost of reformer are avoided. |
Research |
Paired Straight Hearth Furnace |
It enables higher productivity smelting operations. When used as a pre-reducer with a smelter,the combine Process is suitable BF/Coke oven replacement with 30% less energy usage. |
In comparison with Blast Furnace route, the total CO2 emissions per ton of hot metal produced is expected to decrease by one third. |
Demonstration |